Innovate with JHYPCB’s Flex PCB Prototyping Services
Transform your ideas into reality with JHYPCB’s high-quality flex PCB prototyping. Our advanced manufacturing delivers flexible, lightweight, and reliable PCBs for your innovative designs. Get started with rapid prototypes and seamless support.
What Is Flex PCB?
Flex PCBs are an essential component of our common electronics like mobile electronic devices, desktop printers, and hard disks. Comprising of a strong substrate material with or without overlay, Flex PCBs consist of various complex components. Flexible PCB is a printed circuit board that is made of PET (Polyester) or polyimide, with excellent flexibility and high reliability.
Due to the flexibility and advancement in flexible PCB technology, manufacturers of electronics are more inclined to develop the prototype of these devices before manufacturing. This is because the flex PCB prototypes create an avenue for the manufacturers to identify errors and make necessary changes before the product is introduced in the market.
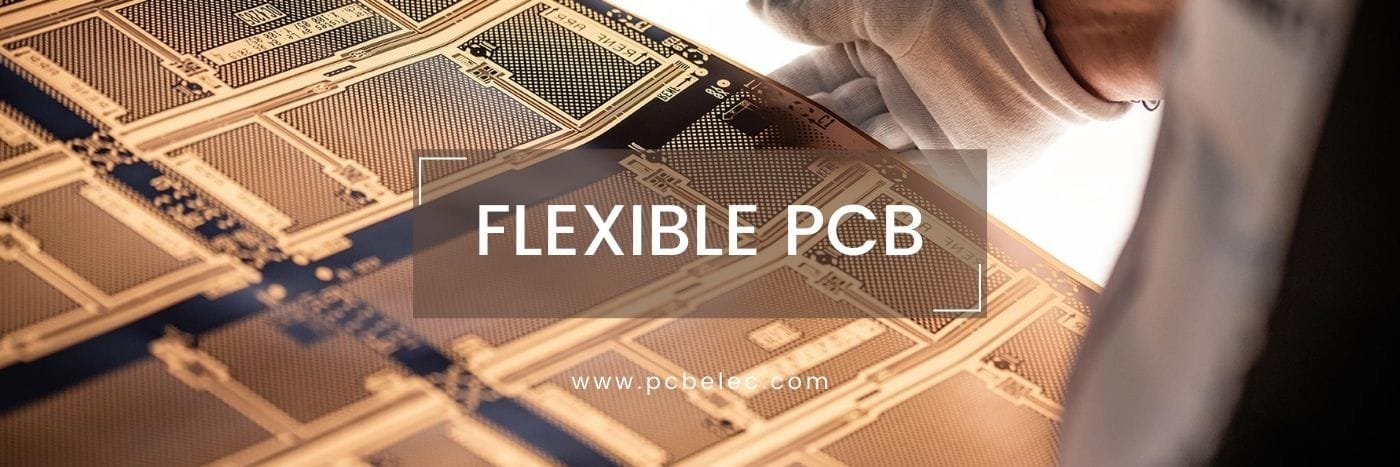
What is Flex PCB Prototyping?
Flex PCB prototyping involves creating small-batch, flexible PCBs to test and refine designs before mass production. Made from materials like polyimide or PET, flex PCBs offer exceptional flexibility, lightweight construction, and durability, ideal for modern electronics like wearables, medical devices, and automotive systems.
Key Benefits of Flex PCB Prototyping
- Lightweight Design: Polyimide-based flex PCBs are significantly lighter than FR4, enabling compact devices.
- Flexibility: Allows complex, bendable designs to fit tight spaces, reducing mechanical footprint.
- Thin Profile: Typically 4.4–10 mils for 2-layer flex PCBs, perfect for miniaturization.
- High-Temperature Resistance: Withstands extreme conditions, oils, gases, and acids.
- Cost Efficiency: Identifies design flaws early, minimizing errors in full-scale production.
- High Signal Integrity: Supports high circuit density with reduced wiring errors.
- Durability: Fewer interconnects enhance resistance to shock and dynamic forces.
Applications of Flex PCB Prototyping
Flex PCB prototypes power innovation across industries:
- Consumer Electronics: Smartphones, smartwatches, and flexible displays.
- Medical Devices: Biocompatible circuits for diagnostics and wearables.
- Automotive: Sensors and control units in space-constrained systems.
- Aerospace: Lightweight, reliable circuits for avionics and satellites.
- Industrial: Robust PCBs for automation and control systems.
- Military & Communications: High-performance circuits for secure, compact applications.
Related Reading: Development and Applications of FPC Flexible PCB

Flex PCB Classifications
- Overview: Features a single conductive layer on a flexible substrate (e.g., polyimide, PET).
- Benefits: Cost-effective, ideal for simple designs with wiring on one side.
- Applications: Basic consumer electronics and low-complexity circuits.
- Overview: Conductive patterns on both sides, connected via metallic holes.
- Benefits: Enhanced design flexibility and component placement.
- Applications: Wearables and compact medical devices.
- Overview: Three or more layers laminated with conductive paths between them.
- Benefits: Improved reliability, thermal conductivity, and assembly performance.
- Applications: Complex electronics like aerospace and industrial systems.
- Overview: Combines flexible and rigid layers for versatile, space-saving designs.
- Benefits: Mechanical stability, reduced connectors, and 3D design flexibility.
- Applications: Automotive, military, and high-reliability systems.
JHYPCB’s Flex PCB Prototyping Process
Our streamlined process ensures precision and quality:
- Design Consultation: Collaborate with our engineers for DFM (Design for Manufacturability) checks to optimize your design.
- Material Selection: Choose from polyimide, PET, or adhesive/non-adhesive flex cores, tailored to your needs.
- Stackup Design: Define layer construction, thickness, and materials (e.g., coverlays, stiffeners) to meet bend and impedance requirements.
- Prototyping: Advanced equipment delivers precise, small-batch flex PCBs with 24–48-hour turnaround options.
- Testing & Validation: Rigorous electrical and mechanical tests ensure reliability and performance.
- Feedback & Iteration: Refine designs based on prototype results for seamless production scaling.
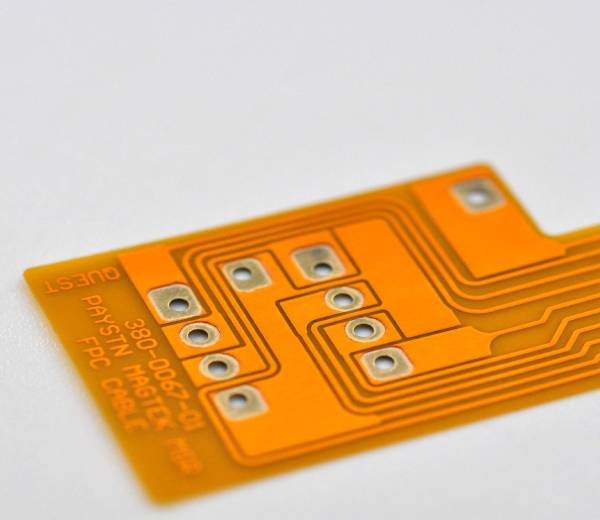
Why Choose JHYPCB for Flex PCB Prototyping?
- Expertise: Over a decade of experience in flexible PCB manufacturing and prototyping.
- Advanced Technology: Cutting-edge equipment for precision and high reliability.
- Comprehensive Services: From PCB prototyping to turnkey PCB assembly and component sourcing.
- Fast Turnaround: Rapid prototyping with 24-hour or same-day delivery options.
- No MOQ: Flexible batch sizes to suit startups and large-scale projects.
- Cost-Effective: Competitive pricing with free DFM checks to optimize designs.
- Global Support: Contact us at sales@pcbjhy.com for personalized service.
Flex PCB Pricing Factors
The cost of flex PCB prototyping depends on:
- Physical Size: Quoted per square inch, with larger boards increasing costs.
- Circuit Construction: Double-sided or multilayer PCBs cost 1.5–2x more than single-layer due to materials and processing complexity.
- Volume: Low-volume orders may incur soft tooling costs for custom designs, but JHYPCB minimizes these with efficient processes.
- Materials: High-quality polyimide, coverlays, or stiffeners (e.g., FR4, aluminum) impact pricing.
- Turnaround Time: Expedited services (e.g., 24-hour delivery) may add a premium.
For accurate pricing, submit your Gerber files and BOM to sales@pcbjhy.com.
Related Reading: Standard PCB Thickness—All You Need To Know
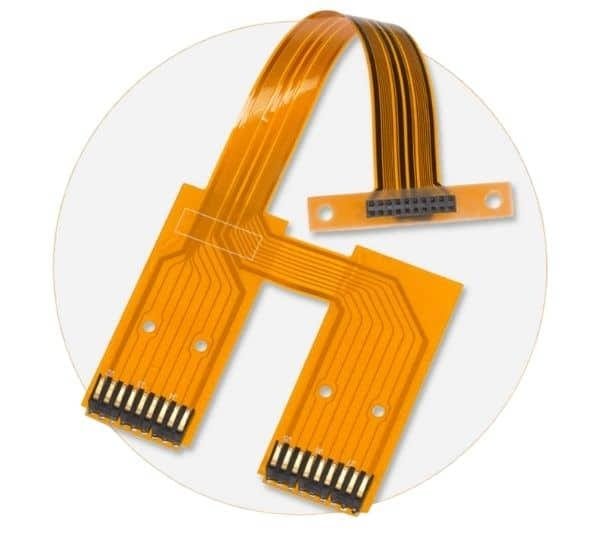
Flex PCB Manufacturing Process
- Material Preparation: Chemically clean production panels to ensure photoresist adhesion.
- Circuit Patterning: Apply photoresist film and etch conductive patterns using rolled or electrodeposited copper.
- Lamination: Bond coverlays or solder masks, ensuring proper adhesion and flexibility.
- Drilling & Plating: Create metallic vias for multilayer or double-sided designs.
- Testing: Conduct electrical, thermal, and mechanical tests to verify performance.
- Finishing: Apply stiffeners, EMI shielding, or pressure-sensitive adhesives as needed.
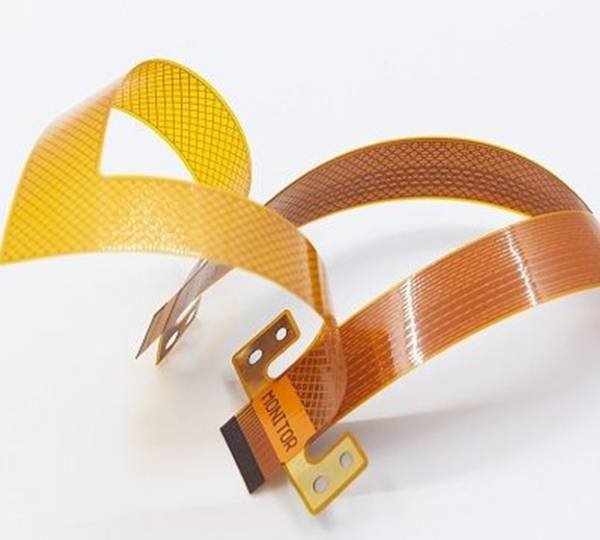
Flex PCB Prototyping FAQs
Most frequent questions and answers
Prototyping verifies design feasibility, identifies errors, and optimizes manufacturability, saving costs before mass production.
Yes, JHYPCB provides free DFM checks to ensure your design is optimized for manufacturing.
Absolutely, we specialize in single-sided, double-sided, and multilayer flex PCBs with high reliability.
We offer rapid prototyping with 24–48-hour delivery for urgent projects, depending on complexity.
Yes, we provide high-quality, reliable prototypes at competitive prices with no MOQ requirements.
Yes, we provide turnkey PCB assembly services, including SMT, THT, and mixed-technology assembly.
Submit your Gerber files and BOM via our online form or email sales@pcbjhy.com.
Get Started with JHYPCB Today
Ready to prototype your next flex PCB project? Trust JHYPCB for fast, reliable, and cost-effective solutions.
Related Reading
- Why is Flexible PCB so Expensive?
- What Is Flexible PCB Coverlay (FPC Cover Layer)?
- The Manufacturing Process Of Double-sided Flexible PCB Coverlay
- What Are The Advantages And Applications Of Rigid-Flex PCBs?
- Rigid PCB vs Flex PCB: What Is The Difference?
- What Are Flexible PCB Stiffeners?
- 16 Factors Affecting The Cost And Price of Flexible PCB
- How to Make Low Cost PCB Prototypes