Table of Contents
Introduction
The double-sided flexible PCB coverlay manufacturing process is a critical step in producing high-performance flexible printed circuit coverlay solutions used in industries like consumer electronics, automotive, and medical devices. A coverlay, unlike a traditional solder mask, provides superior flexibility and durability, protecting copper circuitry while enabling bending and folding. This comprehensive guide explores the step-by-step process of manufacturing double-sided FPC coverlay, from silkscreen printing for FPC coverlay to advanced photo coating FPC process. Whether you’re optimizing FPC coverlay process for smartphones, electric vehicles, or wearable sensors, this article offers expert insights into materials, challenges, innovations, and applications. Read on to discover how coverlay enhances FPC reliability and performance, and download our free checklist, “Optimizing FPC Coverlay Manufacturing: Best Practices,” at JHYPCB to streamline your production.
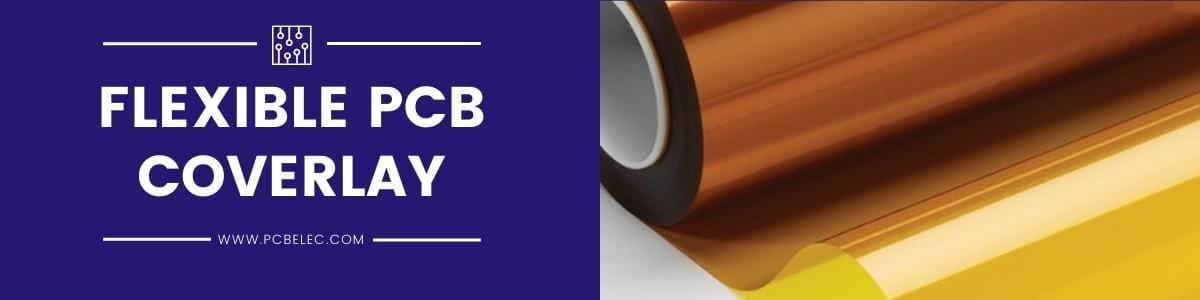
What is a Double-Sided Flexible PCB Coverlay?
A double-sided flexible PCB coverlay is a protective layer applied to the external copper circuits of a flexible printed circuit board. Composed of polyimide or polyester with a flexible adhesive, it serves the same function as a solder mask on rigid PCBs but with enhanced flexibility for dynamic applications. According to industry standards like IPC-6013, coverlay ensures insulation and protection, critical for high-density designs in smartphones, wearables, and automotive electronics. For example, in electric vehicles, double-sided FPCs with coverlay enable lightweight, bendable connections for battery management systems. Understanding coverlay’s role is essential for optimizing the FPC coverlay process and meeting stringent design requirements.
Silkscreen Printing for FPC Coverlay: Process and Limitations
Silkscreen printing is a widely used method in the double-sided flexible PCB coverlay manufacturing process, particularly for cost-sensitive applications like consumer electronics and automotive flexible printed circuits. This technique applies a protective ink layer over the copper circuitry to insulate and shield it, offering a cost-effective alternative to FPC cover film lamination. Below, we explore the silkscreen printing process, its advantages and disadvantages, practical applications, and a visual guide to the workflow.
Process Steps of Silkscreen Printing for FPC Coverlay
- Surface Preparation: Clean the double-sided FPC surface to remove contaminants and oxidation, ensuring proper ink adhesion.
- Ink Selection: Choose UV-curable or heat-curable inks designed for flexible circuits. UV-curable inks cure quickly but offer lower mechanical strength, while heat-curable inks provide better durability.
- Screen Printing: Apply the ink through a stencil onto the FPC using a silkscreen printing machine, leaving openings for connection pads and terminals.
- Curing: Cure the ink using UV light or a batch oven/drying tunnel (20–30 minutes for heat-curable inks).
- Inspection: Check for defects like uneven coating, pinholes, or ink penetration at window ends.
Advantages of Silkscreen Printing
- Cost-Effective: Lower material and processing costs.
- Simple Equipment: Uses standard silkscreen printing equipment.
- Quick Setup: Suitable for low-volume production or prototyping.
Limitations of Silkscreen Printing
- Poor Mechanical Properties: Less durable for frequent bending.
- Chemical Resistance Issues: UV-curable inks may peel during electroless gold plating.
- Thickness Variability: Uneven ink thickness (10–15 µm) in high-density designs.
Use Cases for Silkscreen Printing
- Consumer Electronics: Low-cost devices like remote controls.
- Automotive: Non-dynamic dashboard wiring.
- Prototyping: Rapid, low-cost prototyping.
FPC Cover Film Lamination: Materials and Techniques
In the double-sided flexible PCB coverlay manufacturing process, FPC cover film lamination is the most established technique, using polyimide or polyester films with adhesive to offer superior mechanical strength and flexibility. Below, we explore materials, lamination steps, adhesive considerations, challenges, and a visual guide.
Materials Used in FPC Cover Film Lamination
- Base Film: Polyimide (PI) for thermal stability; polyester (PET) for cost-sensitive applications.
- Adhesive Types:
- Epoxy Adhesive: Semi-cured, 3–4-month shelf life at 5°C.
- Acrylic Adhesive: Stable, >6-month shelf life, higher lamination temperature (160–200°C).
- Release Film: Protects adhesive during storage.
Lamination Process Steps
- Material Preparation: Store films at 5°C, allow to reach room temperature to prevent moisture condensation.
- Window Opening: Use CNC drilling or punching for pad openings.
- Surface Cleaning: Remove oxidation and contaminants.
- Alignment and Temporary Fixing: Manually align film with circuit pattern, secure with soldering iron.
- Lamination: Heat and pressurize at 160–200°C for 1.5–2 hours using a vacuum press.
Acrylic vs. Epoxy Adhesives
- Epoxy: Lower temperature, strong bonding, sensitive to storage.
- Acrylic: Longer shelf life, higher processing cost.
Challenges in FPC Cover Film Lamination
- Adhesive Flow: Overflow or weak bonding due to fluidity.
- Alignment: Wrinkles from manual alignment.
- Moisture Sensitivity: Polyimide absorbs moisture, affecting adhesion.
- Solutions: Use vacuum presses, automated alignment, pre-drying.
Use Cases
- Medical Devices: Wearable monitors.
- Aerospace: Avionics systems.
- Consumer Electronics: Foldable smartphones.

Photo Coating for FPC Coverlay: A Modern Approach
The photo coating FPC process offers precision for high-density FPCs, using light-sensitive materials for fine feature definition. Below, we explore the process, dry film vs. liquid ink, advantages, limitations, and a visual guide.
Photo Coating Process Steps
- Surface Preparation: Clean FPC to ensure adhesion.
- Coating Application:
- Dry Film: Laminate photo-sensitive film using a vacuum machine.
- Liquid Ink: Apply via screen printing or spraying.
- Exposure: Use UV light and photomask for pattern definition.
- Development: Remove unexposed areas with sodium carbonate.
- Post-Curing: Cure in an oven (20–30 minutes).
Dry Film vs. Liquid Ink
- Dry Film: Uniform, high-precision, costly equipment.
- Liquid Ink: Adjustable thickness, cost-effective, uneven in screen printing.
Advantages of Photo Coating
- High Precision: Features down to 100 µm.
- Versatility: Supports dry film and liquid ink.
- Uniform Coating: Spraying ensures consistency.
Limitations
- Mechanical durability less than FPC cover film lamination.
- Higher equipment costs.
- Complex exposure and development control.

Comparison of Coverlay Methods
Selecting the right FPC coverlay process impacts cost and performance. Below is a comparison of silkscreen printing for FPC coverlay, FPC cover film lamination, and photo coating FPC process.
Method | Cost | Durability | Bend Radius | Design Density Support | Applications |
---|---|---|---|---|---|
Silkscreen Printing | Low | Low | Large | Low | Remote controls, dashboard wiring |
Cover Film Lamination | High | High | Small | Medium | Wearable monitors, foldable smartphones |
Photo Coating | Medium | Medium | Medium | High | 5G antennas, medical sensors |
Challenges in FPC Coverlay Processing
The double-sided flexible PCB coverlay manufacturing process faces challenges like adhesive flow, alignment, moisture sensitivity, and peeling.
- Adhesive Flow Management
Fresh films risk overflow; expired films bond poorly.
Solutions: Monitor shelf life, use vacuum presses. - Alignment Issues
Manual alignment causes wrinkles.
Solutions: Use automated vision systems, divide films into smaller sections. - Moisture Sensitivity
Polyimide absorbs moisture.
Solutions: Pre-dry films, use moisture-resistant adhesives. - Peeling During Electroless Gold Plating
UV-curable inks peel in silkscreen printing.
Solutions: Use heat-curable inks, inspect window edges.
Recent Innovations in FPC Coverlay Technology
Innovations like thermoplastic polyimide (TPI), Roll-to-Roll (R2R) automation, and eco-friendly adhesives are transforming the FPC coverlay process.
- Thermoplastic Polyimide (TPI) Films
TPI eliminates adhesives, supports <0.5 mm bend radii, and reduces costs by 15%. - Roll-to-Roll (R2R) Automation
R2R boosts throughput by 20–30% and achieves 20 µm alignment accuracy. - Eco-Friendly Adhesives
Low-VOC adhesives and water-based coatings meet RoHS standards.
Applications of Double-Sided FPC Coverlay in Key Industries
- Consumer Electronics: Foldable Smartphones
FPC cover film lamination supports 200,000 bend cycles, reducing device thickness by 20%. - Automotive: Battery Management Systems
FPC cover film lamination reduces wiring weight by 30%, increasing BMS lifespan by 10%. - Medical Devices: Wearable Sensors
Photo coating FPC process improves sensor accuracy by 15% with biocompatible coverlay.

FAQs
What Causes Coverlay Peeling in FPC Manufacturing?
Peeling occurs due to poor chemical resistance in silkscreen printing. Solutions: Use heat-curable inks, ensure thorough curing.
How to Choose the Right Coverlay for High-Density Designs?
Photo coating supports fine features (100 µm); cover film lamination with TPI suits dynamic designs.
What Is the Shelf Life of FPC Cover Film?
Epoxy: 3–4 months at 5°C; acrylic: >6 months.
Why Does Silkscreen Printing Have Uneven Coating Issues?
Directionality causes skip printing. Solutions: Use two passes, consider photo coating.
Can FPC Coverlay Be Used in Harsh Environments?
FPC cover film lamination withstands 300°C and chemicals.
Conclusion
The double-sided flexible PCB coverlay manufacturing process powers industries like consumer electronics, automotive, and medical devices. Silkscreen printing for FPC coverlay offers cost-effective protection, FPC cover film lamination ensures durability, and photo coating FPC process delivers precision. Innovations like TPI and R2R automation enhance efficiency, addressing challenges like peeling and alignment. Contact our team to elevate your flexible printed circuit coverlay production.
Related Reading
- Double-Sided PCB Manufacturing Process
- Single-Sided Vs. Double-Sided PCB
- Find Out Now, What Should You Do For Fast PCB Classification?
- A Complete Guide To Single-Sided Flex Circuits
- A Completed Guide Of Double-Sided Flexible PCB
- Everything You Need To Know About Multilayer Flexible PCB
- What is Flexible PCB Prototype?
- What Are Flexible PCB Stiffeners?
- The Benefits Of Using Double Sided PCBs
- Custom Flex PCB:Tailored Solutions for Your Applications
- Flexible PCB Manufacturing: A Guide to Fabrication and Assembly
- How to Select the Right Flexible PCB Manufacturer for Your Product: A 6-Step Guide
- What Are The Types of Flexible Circuit Boards?
- Top Applications of Flexible Printed Circuit Boards in 2024
- Flexible PCB Cost: Why It’s More Expensive and How to Reduce It
- What Is Flexible PCB Coverlay (FPC Cover Layer)?
- Rigid PCB vs Flex PCB: What Is The Difference?
- 16 Factors Affecting The Cost And Price of Flexible PCB
- Development and Applications of FPC Flexible PCB
- Complete Introduction of Flexible Circuit Board Materials