Table of Contents
Surface Mount Technology (SMT) is the backbone of modern electronics manufacturing, enabling the creation of compact, high-performance, and reliable PCBs. Unlike traditional through-hole methods, SMT allows electronic components to be mounted directly onto the PCB surface, reducing size, improving efficiency, and enhancing durability. The success of SMT assembly hinges on the careful selection and application of key materials, including solder paste, flux, adhesives, cleaning agents, and solder mask. This guide explores these critical materials, their roles in the SMT process, and best practices for optimizing PCB assembly.
Why SMT Materials Matter
The choice of materials in SMT directly impacts the quality, reliability, and cost-effectiveness of the final PCB. From ensuring strong electrical connections to maintaining component stability during high-speed production, each material plays a specialized role. Understanding these materials empowers manufacturers to meet stringent industry standards, such as IPC J-STD-005 for solder paste or RoHS for environmental compliance, while addressing challenges like miniaturization and thermal management.
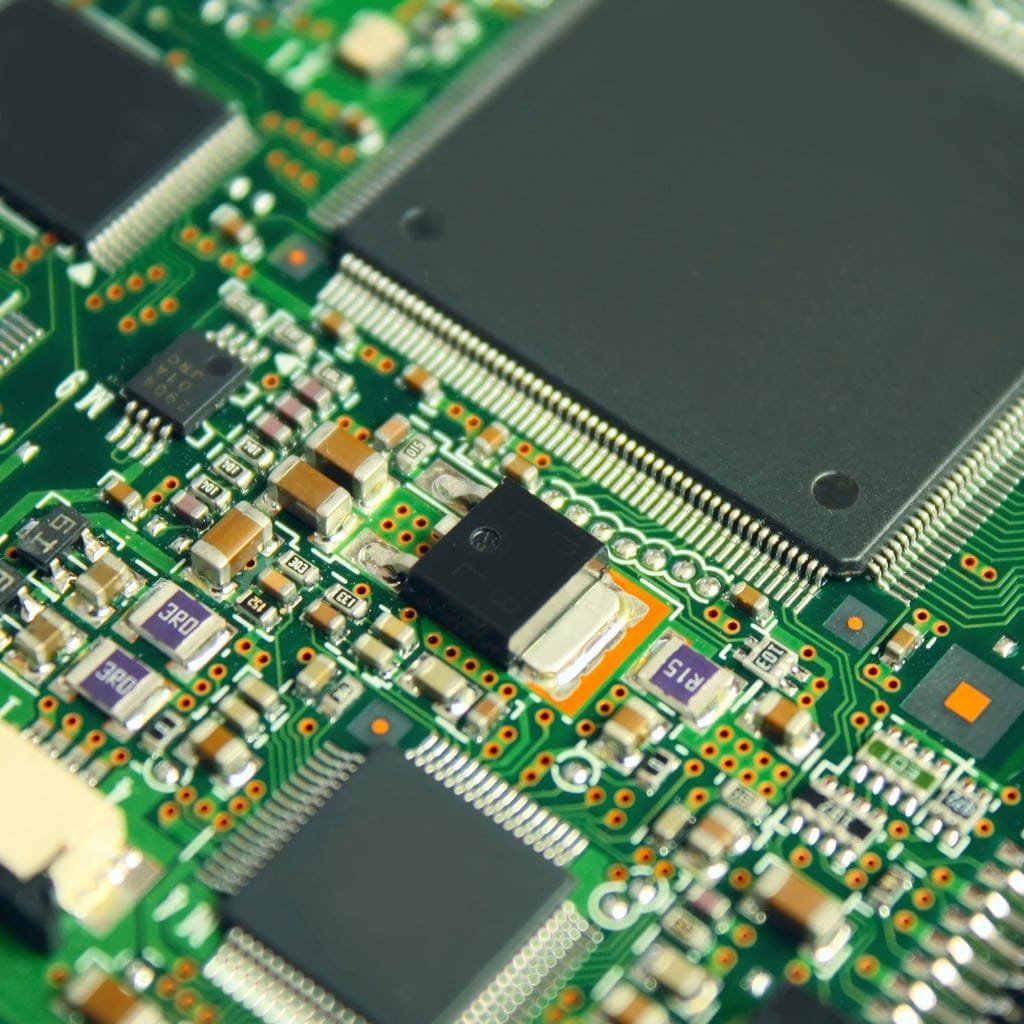
Solder Paste: The Backbone of SMT Assembly
Solder paste is the cornerstone of SMT, serving as both an adhesive and a conductive medium to secure surface-mount devices (SMDs) to the PCB. It consists of metal alloy particles suspended in a flux medium, which facilitates smooth soldering during reflow or wave soldering processes. The most common alloy, SAC305 (96.5% tin, 3.0% silver, 0.5% copper), is widely used for its lead-free composition, compliance with RoHS regulations, and relatively low melting point of approximately 217°C.
Key Considerations for Solder Paste
- Alloy Composition: Different alloys suit specific applications. For example, Sn63/Pb37 (63% tin, 37% lead) has a lower melting point (183°C), making it suitable for temperature-sensitive components, but its use is declining due to environmental concerns.
- Particle Size: For high-density PCBs, such as those in smartphones or wearables, finer particle sizes (Type 4 or 5) ensure precise application through stencil printing.
- Flux Type: No-clean, water-soluble, or rosin-based fluxes are chosen based on the cleaning requirements and soldering environment.
In practice, solder paste is applied using a stencil to deposit precise amounts onto PCB pads. During reflow soldering, the paste melts, forming reliable electrical and mechanical connections. For instance, in automotive electronics, SAC305 solder paste ensures robust joints that withstand thermal cycling and vibration.
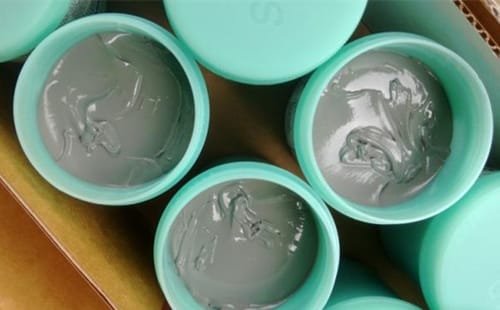
Flux: Ensuring Clean and Reliable Soldering
Flux is a critical component of solder paste, but it also serves as a standalone material in some SMT processes. Its primary role is to clean metal surfaces by removing oxides and contaminants, ensuring the molten solder wets the PCB pads and component leads effectively. Flux also prevents oxidation during soldering, enhancing joint reliability.
Types of Flux
- Rosin-Based Flux: Commonly used for its mild cleaning properties and minimal residue.
- Water-Soluble Flux: Offers strong cleaning capabilities but requires thorough post-soldering cleaning.
- No-Clean Flux: Leaves minimal residue, reducing cleaning needs but requiring careful selection to avoid reliability issues.
Flux is particularly vital in high-reliability applications, such as medical devices, where clean solder joints prevent electrical failures. However, improper flux selection can lead to issues like solder balling or incomplete wetting, so compatibility with the solder paste and soldering process is essential.

Adhesives: Securing Components in High-Speed Processes
Adhesives play a pivotal role in SMT, especially in double-sided PCB assembly or wave soldering. They temporarily secure SMDs to the PCB before soldering, preventing displacement during high-speed production or thermal processing. SMT adhesives are typically dispensed as dots or lines using automated equipment and cure rapidly under heat or UV light.
Benefits of SMT Adhesives
- Component Stability: Ensures SMDs remain in place during reflow or wave soldering.
- Versatility: Suitable for a wide range of component sizes, from tiny chip resistors to larger ICs.
- Process Efficiency: Enables double-sided assembly, maximizing PCB real estate.
In consumer electronics, adhesives are critical for assembling compact devices like smartwatches, where components must be precisely positioned on densely populated boards. Choosing the right adhesive involves balancing curing time, bond strength, and compatibility with soldering temperatures.
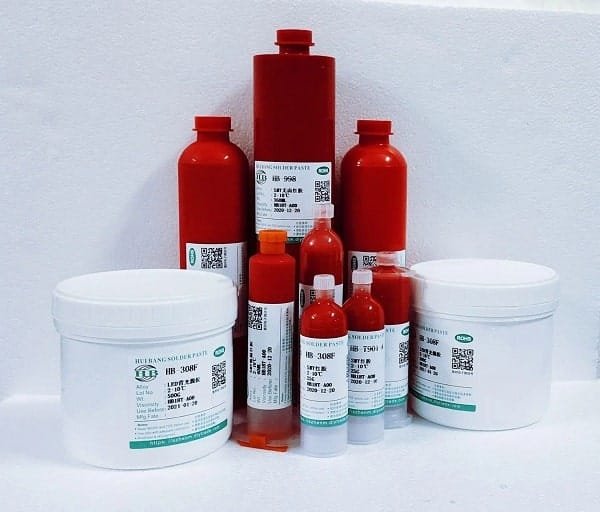
Cleaning Agents: Maintaining PCB Performance and Longevity
After soldering, residues from solder paste, flux, or adhesives may remain on the PCB, potentially compromising electrical performance or long-term reliability. Cleaning agents, often alcohol-based or water-based solutions, are used to remove these residues and ensure a pristine board surface.
Cleaning Agent Applications
- Post-Soldering Cleaning: Removes flux residues to prevent corrosion or electrical shorts.
- Stencil Cleaning: Keeps SMT stencils free of solder paste buildup, ensuring consistent printing.
- Conformal Coating Preparation: Cleans surfaces before applying protective coatings.
In aerospace electronics, where reliability is paramount, cleaning agents are used to meet stringent cleanliness standards, such as those outlined in IPC-CH-65. Alcohol-based cleaners, like isopropyl alcohol (IPA), are popular for their effectiveness and fast evaporation, while water-based cleaners are preferred for environmentally sensitive applications.
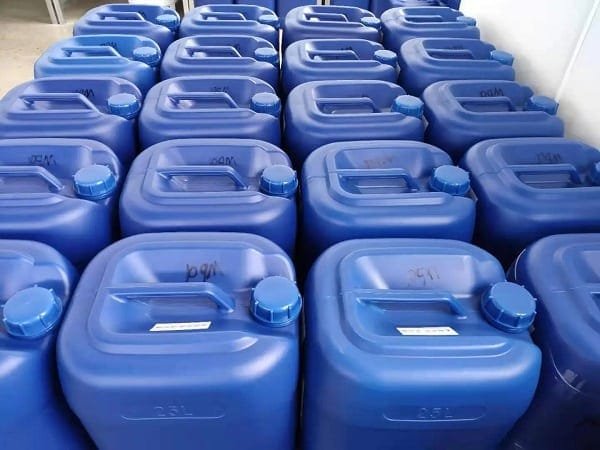
Solder Mask: Protecting and Enhancing PCB Reliability
Solder mask, though often overlooked, is a critical material in SMT assembly. This thin polymer layer is applied to the PCB surface, leaving only the pads exposed for soldering. It protects copper traces from oxidation, prevents solder bridges, and enhances the board’s durability.
Types of Solder Mask
- Liquid Photoimageable (LPI): The most common type, offering high precision for fine-pitch PCBs.
- Dry Film: Used for simpler boards with less stringent requirements.
- Epoxy-Based: Provides robust protection for harsh environments, such as automotive applications.
Solder mask also improves the aesthetic and functional quality of PCBs, as seen in high-end consumer electronics where green, blue, or black masks are used for branding and reliability.
Emerging Trends in SMT Materials
As electronics continue to evolve, so do SMT materials. Key trends include:
- Low-Temperature Solder Paste: Reduces energy consumption and supports temperature-sensitive components.
- Nano-Solder Paste: Enhances joint strength for ultra-fine-pitch applications in 5G and IoT devices.
- Eco-Friendly Cleaning Agents: Align with environmental regulations and reduce waste.
Keeping abreast of these trends ensures manufacturers remain competitive in industries like automotive, telecommunications, and medical electronics.
FAQ: Common Questions About SMT Materials
What is the difference between leaded and lead-free solder paste?
Leaded solder paste (e.g., Sn63/Pb37) has a lower melting point (183°C) and is easier to work with, but lead-free options (e.g., SAC305) are preferred for environmental compliance and durability in high-reliability applications.
How do I choose the right flux for my SMT process?
Consider the soldering method, component sensitivity, and cleaning requirements. No-clean flux is ideal for minimal post-processing, while water-soluble flux suits high-cleanliness applications.
Conclusion: Building Reliable PCBs with SMT Materials
Selecting the right materials for SMT assembly is crucial for producing high-quality, reliable, and efficient PCBs. Solder paste forms strong connections, flux ensures clean joints, adhesives secure components, cleaning agents maintain performance, and solder mask protects the board. By understanding these materials and their applications, manufacturers can optimize their SMT processes and meet the demands of modern electronics.
For more insights on PCB assembly or to explore advanced SMT solutions, visit our PCB Assembly Services or contact our team of experts today.