Table of Contents
Introduction
Ensuring a clean printed circuit board assembly (PCBA) is critical for performance, reliability, and longevity. From removing flux residues to preparing for conformal coating, proper cleaning can make or break your PCB’s quality. In this guide, we’ll explore why cleaning PCBAs matters and the safest, most effective methods to achieve spotless results, whether for military, medical, or consumer electronics applications.
Why clean PCBA?
During PCB assembly, contaminants such as operator fingerprints, factory dust, flux residues, and oxides inevitably accumulate on the board’s surface. These pollutants not only make the PCBA unsightly but can also compromise its functionality and longevity. Here’s why cleaning PCBAs is a non-negotiable step:
- Enhanced Reliability for High-Precision PCBs
Military and medical PCBs operate in extreme environments (e.g., high temperature or humidity). Contaminants like dust or flux residues can absorb moisture, damage the solder mask, and cause short circuits. Clean PCBAs are more reliable and durable, ensuring consistent performance. For example, a medical device manufacturer reduced failure rates by 30% after implementing thorough PCBA cleaning for their sensor boards. - Improved Conformal Coating Adhesion
Conformal coating protects PCB components from environmental damage. Cleaning the PCBA beforehand increases coating adhesion by 50% and ensures uniformity. Uncleaned surfaces may develop cracks, reducing the coating’s effectiveness. - Removal of Post-Soldering Contaminants
Even in the cleanest assembly plants, soldering leaves flux residues and other contaminants. These can corrode components or affect electrical performance if not removed.
Cleaning PCBAs before packing and shipping is essential to meet industry standards, such as IPC-A-610 for Class 3 PCBs, used in critical applications.

Best Methods for Cleaning PCB Assembled Boards
To avoid damaging sensitive components, selecting the right cleaning method and solvent is crucial. Below, we detail three effective methods: semi-automatic, fully automatic, and manual cleaning, each suited for different production scales and requirements.

1. Semi-Automatic Online Cleaning: Fast and Safe for Small Batches
Semi-automatic online cleaning machines are ideal for small to medium batches of PCBAs. These systems are fast, safe, and integrate seamlessly into production lines.
- How It Works
A semi-automatic cleaner uses a clamp to secure the PCBA and applies water-based or solvent-based cleaning agents. The process includes cleaning, rinsing, and drying stages, ensuring thorough contaminant removal. - Advantages
- Safe for delicate components when using compatible solvents.
- Faster than manual cleaning, with consistent results.
- Suitable for small-scale production or prototype testing.
- Limitations
- Requires specific solvents compatible with the PCBA’s surface finish and solder mask.
- Not cost-effective for large-scale production.
- Best Use Case
Semi-automatic cleaning is perfect for low-volume, high-precision PCBAs, such as those used in aerospace or medical prototyping.
2. Fully Automatic Online Cleaning: High-Efficiency for Large-Scale Production
Fully automatic online cleaning machines are designed for high-volume PCBA cleaning, offering speed, precision, and scalability.
- How It Works
The machine automates water-based chemical cleaning, rinsing, and drying. PCBAs move through a conveyor system, ensuring uniform cleaning. Solvents must be compatible with components, PCB surface finishes (e.g., HASL, ENIG), and solder masks. - Advantages
- Highly efficient for large batches, reducing labor costs.
- Suitable for critical applications like aerospace, military, and medical PCBs.
- Consistent cleaning quality with minimal human intervention.
- Limitations
- Expensive equipment and solvent costs.
- Requires regular maintenance and trained operators.
- Automated Cleaning Steps
- Prepare Deionized Water: Use an electrodialysis device and ion exchange resin tank to produce high-purity deionized water (conductivity <1 µS/cm).
- Test Conductivity: Verify water quality with a conductivity tester to ensure it meets cleaning standards.
- Load Water into Machine: Introduce deionized water into the cleaning machine’s storage tank.
- Set Parameters: Configure washing and rinsing rooms to 60 ± 10°C to balance effective cleaning and component safety. Set the drying room to 60-90°C based on PCBA complexity (e.g., lower for high-density boards).
- Adjust Chain Speed: Set conveyor speed to 50-150 cm/min to optimize cleaning time.
- Store Cleaned PCBAs: Place cleaned PCBAs in clean, dust-free anti-static containers to prevent secondary contamination.
- Best Use Case
Fully automatic cleaning is ideal for high-volume production, such as consumer electronics or automotive PCBs, where consistency and speed are critical.
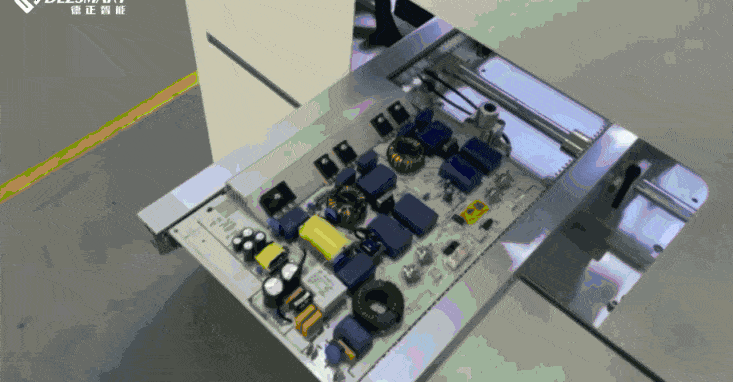
3. Manual Cleaning: Cost-Effective for Prototypes and Small Runs
Manual cleaning is a low-cost option for small batches or prototypes, using water-based or solvent-based cleaning agents like IPA (isopropyl alcohol) or VIGON EFM.
- How It Works
Operators manually clean PCBAs in a controlled environment, using brushes, wipes, and solvents. This method is labor-intensive but offers flexibility for small-scale projects. - Advantages
- Low equipment costs, ideal for startups or small workshops.
- Suitable for delicate or custom PCBAs requiring careful handling.
- Limitations
- Lower efficiency and inconsistent cleaning compared to automated methods.
- Cannot effectively clean dense components or tight gaps (e.g., under IC pins).
- Manual Cleaning Steps
- Apply Cleaning Agent: Use 10 ml of IPA or VIGON EFM per 4 square inches of PCBA surface, spraying or dipping as needed.
- Brush Surface: Gently scrub with a soft, short-bristle brush for 10 seconds to remove flux and contaminants.
- Rinse with Deionized Water: Apply 10 ml per 4 square inches to wash away residues.
- Wipe Dry: Use a clean, lint-free cloth to remove excess water.
- Inspect Cleanliness: Visually check for residues under a magnifying glass or use an ionic contamination tester (<1.56 µg/cm² NaCl equivalent).
- Dry with Air Gun: If needed, use a clean air gun to dry the PCBA.
- Store Properly: Place PCBAs in sealed bags with desiccants if not immediately coated or assembled.
- Best Use Case
Manual cleaning suits prototype development or small-scale production where cost is a priority.



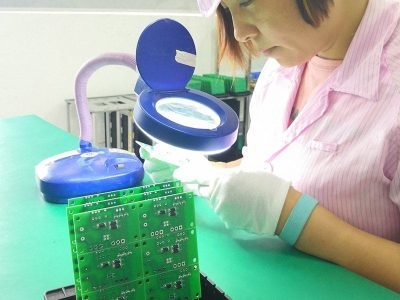
Environmental and Safety Considerations
When cleaning PCBAs, prioritize eco-friendly practices and operator safety:
- Choose Low-VOC Solvents: Opt for water-based or low-volatile organic compound (VOC) cleaning agents to minimize environmental impact.
- Ensure Operator Safety: Provide gloves, protective eyewear, and well-ventilated workspaces to reduce exposure to chemical fumes.
- Dispose of Waste Properly: Follow local regulations for disposing of used solvents and contaminated water to avoid environmental harm.
FAQ: Common PCBA Cleaning Questions
How can I verify if a PCBA is clean enough?
Inspect the PCBA under a magnifying glass for visible residues. For critical applications, use an ionic contamination tester to ensure residues are below 1.56 µg/cm² NaCl equivalent.
What happens if residues persist after cleaning?
Persistent residues may indicate incompatible solvents or insufficient cleaning time. Adjust the solvent type (e.g., switch to a stronger water-based cleaner) or extend cleaning duration. For manual cleaning, focus on hard-to-reach areas with a finer brush.
Can I skip cleaning before conformal coating?
No. Uncleaned PCBAs can cause coating adhesion issues, leading to cracks or peeling, which compromise protection.
Visualizing the Cleaning Process
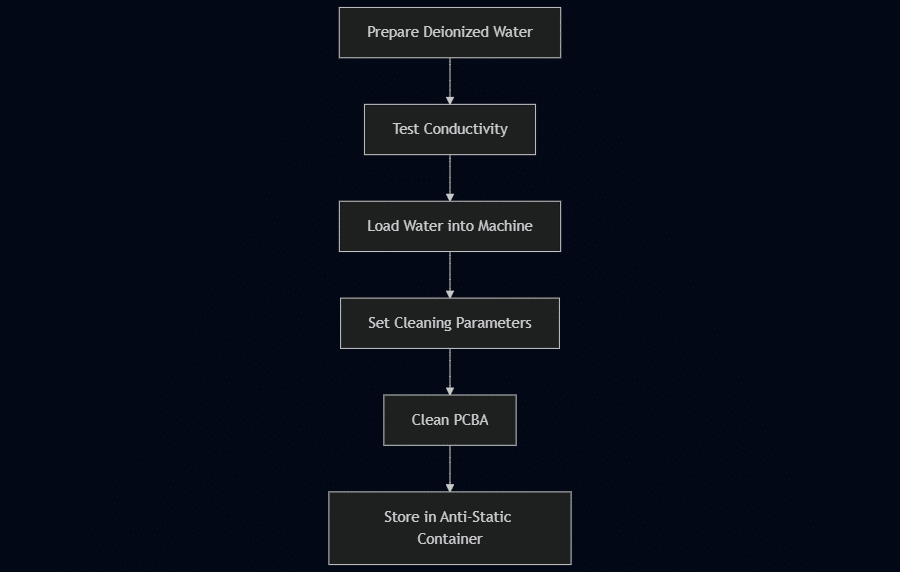
Conclusion
Cleaning PCB assembled boards is essential for ensuring reliability, performance, and longevity. Whether you choose semi-automatic cleaning for small batches, fully automatic systems for high-volume production, or manual methods for prototypes, selecting the right tools and solvents is key. By following industry best practices and prioritizing eco-friendly solutions, you can achieve spotless PCBAs ready for conformal coating or final assembly.
Ready to optimize your PCBA cleaning process? Explore JHYPCB’s PCB assembly services for high-quality, reliable solutions.
Related Reading
- How To Clean The Solder Paste On SMT Stencil
- What is the difference between wave soldering and reflow soldering?
- SMT PCB Assembly Manufacturing Process Introduces
- Materials Used in Surface Mount Technology
- Testing & Inspection Methods For PCB And PCBA
- X-Ray Inspection In PCB Assembly
- How to Solder On Flex PCB?
- Complete Introduction To Flexible PCB Assembly Process