Introduction to PCB OSP Surface Finish
In the world of PCB manufacturing, surface finishing is a critical step that ensures the reliability and performance of electronic devices. Applied after the solder mask, surface finishes protect copper traces from oxidation and provide a solderable surface for component attachment. Among the various options—such as Electroless Nickel Immersion Gold (ENIG), Immersion Tin, and Hot Air Solder Leveling (HASL)—Organic Solderability Preservative (OSP) stands out for its cost-effectiveness and environmental benefits. This guide explores OSP surface finish, detailing its process, advantages, limitations, and best practices for storage and assembly, helping you make informed decisions for your PCB projects.
Table of Contents
What is PCB Surface Finish?
A PCB surface finish acts as a protective layer between the PCB’s copper traces and electronic components, ensuring reliable soldering and preventing oxidation. Surface finishes can be metallic (e.g., ENIG, Immersion Silver) or organic (e.g., OSP). The choice of finish significantly impacts PCB performance, cost, and compliance with environmental regulations like RoHS (Restriction of Hazardous Substances) and WEEE (Waste from Electrical and Electronic Equipment).
The primary functions of a PCB surface finish are:
- Creating a solderable surface for component attachment.
- Protecting exposed copper traces from oxidation, which can degrade performance.
Selecting the right surface finish is as crucial as choosing the PCB material itself. It requires balancing performance needs, manufacturing constraints, and regulatory compliance, often with guidance from your PCB manufacturer.

Factors Influencing PCB Surface Finish Choice
Choosing a PCB surface finish involves evaluating several factors to ensure compatibility with your project’s requirements:
- Application Needs: High-frequency circuits may require ENIG for superior conductivity, while consumer electronics may prioritize cost-effective OSP.
- Environmental Compliance: RoHS and WEEE regulations favor lead-free finishes like OSP.
- Cost Considerations: OSP is more affordable than ENIG or Immersion Silver.
- Assembly Process: The finish must support reflow or wave soldering techniques.
- Component Types: Fine-pitch components or Ball Grid Arrays (BGAs) benefit from OSP’s flatness.
- Shelf Life: OSP’s shorter shelf life may affect long-term storage plans.
Collaborating with your PCB manufacturer helps align the finish with your project’s technical and regulatory needs.
What Is OSP Surface Finish?
Organic Solderability Preservative (OSP) is a water-based, organic coating applied to copper surfaces to prevent oxidation and ensure solderability. Unlike metallic finishes, OSP creates a thin, transparent protective layer, making it an eco-friendly and cost-effective choice for lead-free soldering. OSP is widely used in consumer electronics, automotive, and industrial applications due to its simplicity and alignment with environmental standards.
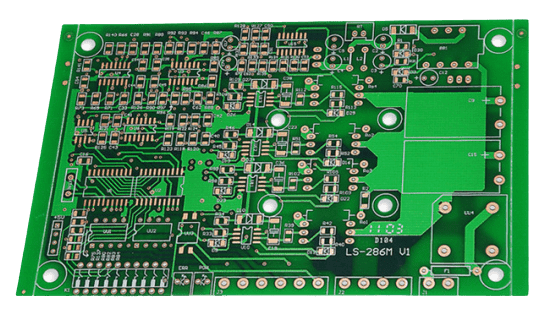
OSP Surface Finish Manufacturing Process

The OSP application process is precise, ensuring a uniform protective coating on copper surfaces. It involves four key steps:
- Cleaning: Removes organic contaminants, oils, and oxides to ensure a uniform copper surface for coating adhesion.
- Topography Enhancement: Micro-etching roughens the copper to improve OSP bonding, preventing oxidation.
- De-ionization Washing: Eliminates residual ions that could contaminate the OSP solution.
- Film Formation: Applies the OSP coating, followed by de-ionized rinsing at a pH of 4.0–7.0 to prevent tarnishing.
Regular monitoring of these steps ensures consistent quality and performance.
Advantages of OSP Surface Finish
OSP offers distinct advantages, making it a preferred choice for many PCB applications:
- Superior Flatness: Ideal for fine-pitch components and BGAs.
- Cost-Effective: Lower production costs compared to ENIG or Immersion Silver.
- Eco-Friendly: Uses water-based compounds, complying with RoHS and WEEE.
- Reworkable: Allows easy reapplication of the coating.
- Simple Process: Supports horizontal production lines and lead-free soldering.

Disadvantages of OSP Surface Finish
Despite its benefits, OSP has limitations that may affect its suitability:
- Sensitive Handling: Requires gloves to avoid contamination or scratches.
- Short Shelf Life: Typically 6–12 months, unsuitable for extended storage.
- Limited Thermal Cycles: Not ideal for multiple soldering processes.
- Inspection Challenges: Transparent coating complicates visual inspection.
- Cleaning Sensitivity: Misprinted solder paste removal can damage the OSP layer.
- Baking Risks: Pre-use baking may degrade the coating.
Benefits of OSP Surface Finish
- Optimal Soldering: Ensures reliable solder joints during assembly.
- Repair Flexibility: Damaged OSP coatings can be reworked easily.
- Environmental Compliance: Uses non-toxic, water-based compounds.
- Cost Efficiency: Simplifies manufacturing, reducing fabrication costs.
- Storage Suitability: Performs well under controlled conditions (vacuum, low humidity).
How To Store OSP PCB?
Proper storage prevents oxidation and maintains OSP PCB solderability:
- Use vacuum packaging with desiccants and humidity indicators.
- Insert release paper between PCBs to prevent friction damage.
- Avoid direct sunlight exposure.
- Maintain 30–70% relative humidity and 15–30°C temperature.
- Limit storage to 12 months for optimal performance.
Key Considerations for Assembling OSP PCBs
When assembling OSP PCBs, consider:
- Solderability: Ensure the OSP coating supports efficient soldering to copper.
- Process Duration: OSP application is faster than HASL, saving production time.
- Reliability: Verify the coating’s durability for your application.
- Corrosion Resistance: OSP is less prone to corrosion than Immersion Silver.
- Layout Compatibility: Optimize PCB design for OSP’s flatness and sensitivity.

Why Is OSP Surface Finish Popular?
Before 2005, Lead HASL was the standard for PCB surface finishing due to its reliability and low cost. However, environmental concerns and regulations like RoHS and WEEE pushed manufacturers toward lead-free alternatives. OSP emerged as a cost-effective, eco-friendly solution, using a water-based organic coating that avoids toxic metals. Its affordability, compatibility with lead-free soldering, and suitability for copper pad applications have made it a top choice for consumer electronics, automotive, and industrial PCBs. Despite its limitations, OSP’s balance of performance and sustainability drives its widespread adoption.
Comparison of OSP with Other Surface Finishes
To help you choose the right surface finish, here’s a comparison of OSP with other common finishes:
Feature | OSP | ENIG | Immersion Silver | Lead-Free HASL |
---|---|---|---|---|
Cost | Low | High | Moderate | Moderate |
Flatness | Excellent | Good | Good | Poor |
Shelf Life | 6–12 months | 12+ months | 6–12 months | 12+ months |
Environmental Impact | Eco-friendly (RoHS-compliant) | Moderate | Moderate | Moderate |
Solderability | Good | Excellent | Excellent | Good |
Thermal Cycles | Limited | High | Moderate | High |
Conclusion
OSP surface finish is a cost-effective, eco-friendly solution for PCB manufacturing, offering excellent flatness and reliable solderability. While its short shelf life and sensitive handling require careful management, its advantages make it ideal for many applications, from consumer electronics to industrial devices. By understanding OSP’s manufacturing process, benefits, and storage requirements, you can optimize your PCB projects for performance, cost, and environmental compliance.