Table of Contents
Introduction to Rigid-Flex PCB
Rigid-flex PCBs combine the strengths of rigid and flexible circuits, creating a hybrid solution that supports complex, high-density electronic designs. By integrating rigid and flexible substrates through plated through holes (PTH), these boards enable three-dimensional (3D) assembly, making them ideal for industries like aerospace, medical devices, and consumer electronics. In this guide, we explore the essentials of rigid-flex PCB stackup, including its features, types, design considerations, and real-world applications.

What is Rigid-Flex PCB Stackup?
A rigid-flex PCB stackup refers to the arrangement of conductive and insulating layers in a hybrid circuit board. The stackup includes both rigid sections (typically made of FR4) and flexible sections (made of polyimide or similar materials), interconnected to form a single, cohesive unit. This unique structure allows rigid-flex PCBs to bend and fold, accommodating compact and intricate designs while maintaining reliability.
Key Features of Rigid-Flex PCB Stackup
- Fewer Solder Joints and Connectors: Reduces points of failure, enhancing reliability.
- Thinner Board Thickness: Enables lightweight and compact designs.
- Superior Thermal Performance: Efficient heat dissipation for high-performance applications.
- High Aspect Ratio: Supports complex, high-density interconnect (HDI) designs.
- 3D Flexibility: Allows folding and bending for space-constrained applications.
Types of Rigid-Flex PCB Stackup
Rigid-flex PCBs come in various configurations, each suited to specific applications:
- Single-Sided Rigid-Flex PCB
Features a single conductive layer, ideal for simple, cost-effective designs like wearable devices. - Double-Sided Rigid-Flex PCB
Includes two conductive layers, offering increased routing flexibility for moderately complex applications. - Multi-Layer Rigid-Flex PCB
Combines multiple rigid and flexible layers (e.g., 4-layer or 6-layer stackups) for high-density designs, such as those in aerospace or medical equipment.
Example: 4-Layer Rigid-Flex PCB Stackup
A typical 4-layer rigid-flex PCB includes two flexible layers (polyimide-based) and two rigid layers (FR4-based). The flexible section allows bending, while the rigid section supports components and connectors. Below is a simplified diagram of a 4-layer stackup:
Layer | Material | Function |
---|---|---|
Top Rigid Layer | FR4 | Component mounting |
Flexible Layer 1 | Polyimide | Signal routing |
Flexible Layer 2 | Polyimide | Signal routing |
Bottom Rigid Layer | FR4 | Connector support |
Rigid-Flex Stackup Example
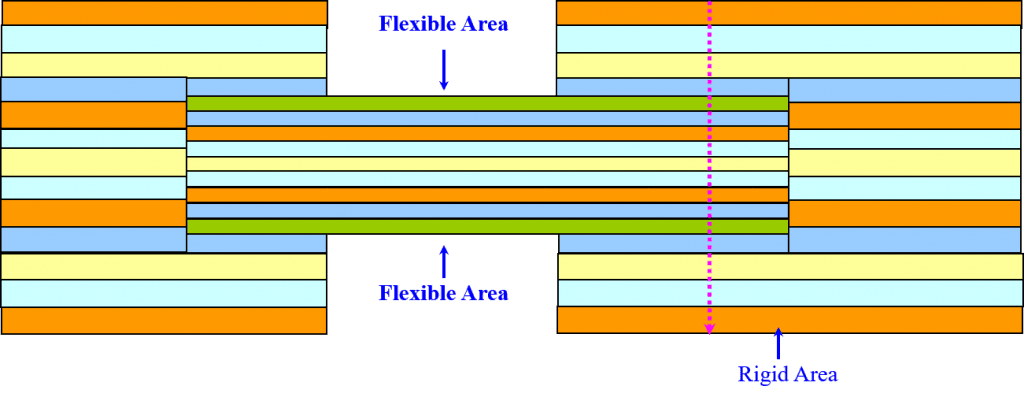
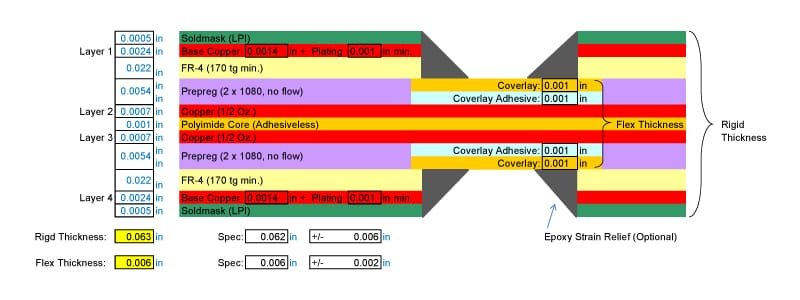
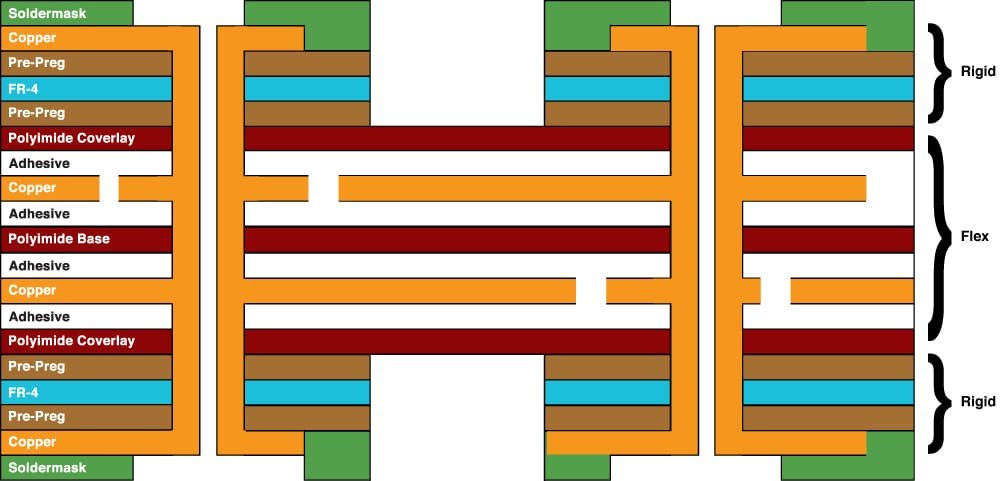
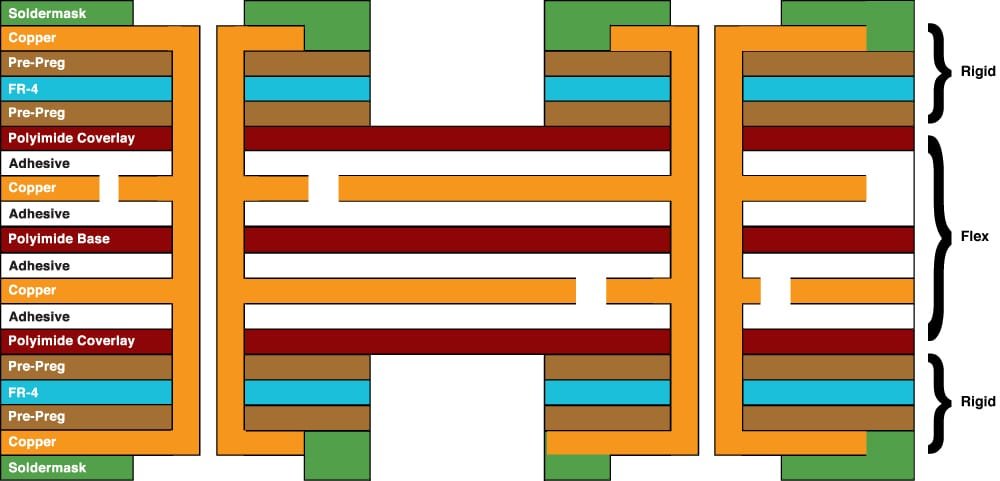
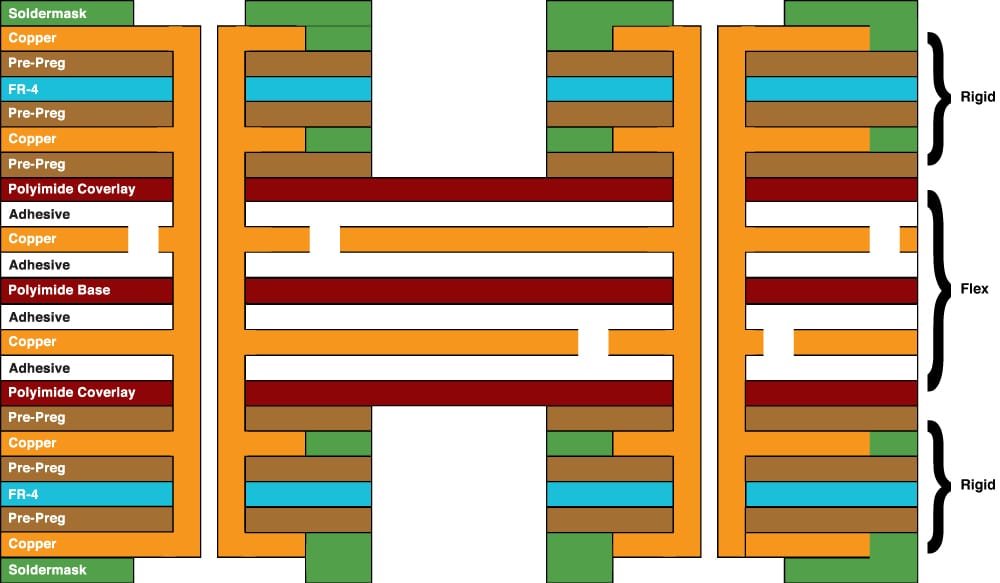
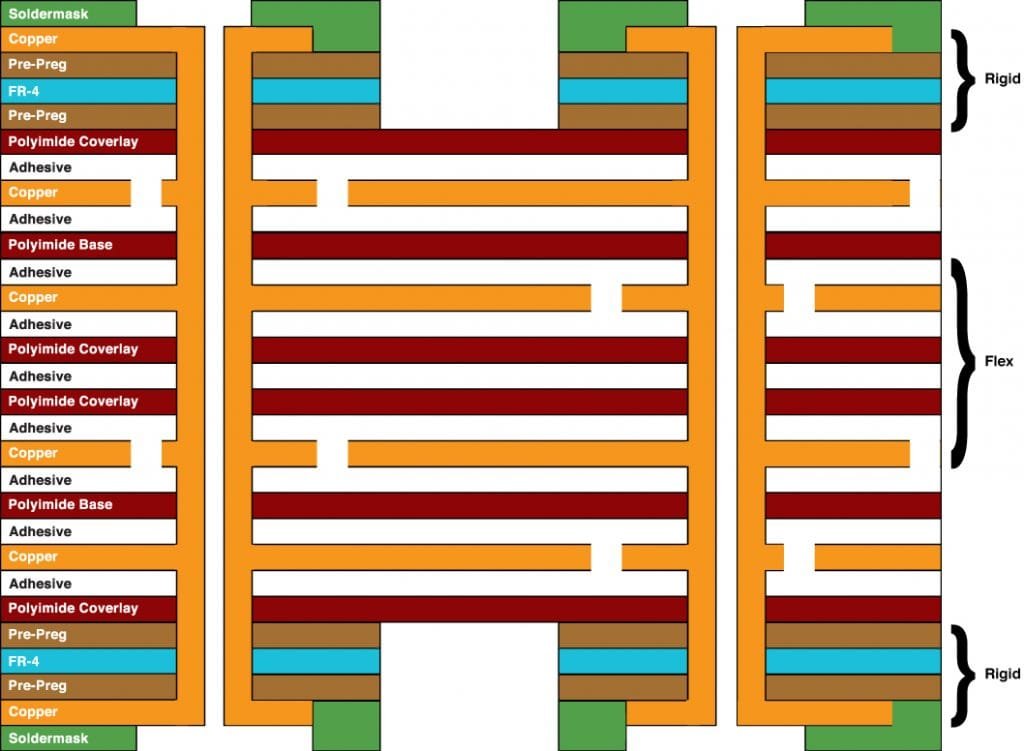
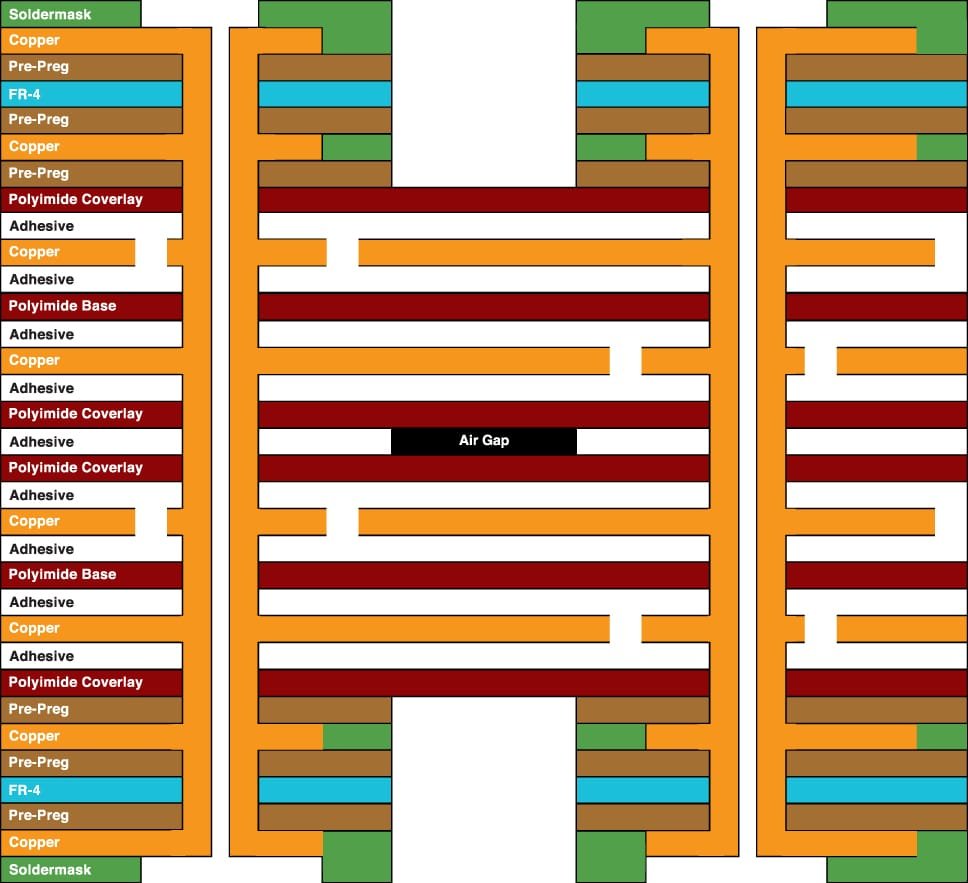

Design Considerations for Rigid-Flex PCB Stackup
Designing a rigid-flex PCB stackup requires careful planning to ensure reliability and performance:
- Material Selection: Choose high-quality polyimide for flexible layers and FR4 for rigid layers to balance durability and flexibility.
- Bend Radius: Maintain a minimum bend radius (typically 10x the thickness of the flex layer) to prevent cracking.
- Via Placement: Use staggered vias in flexible sections to enhance reliability.
- Thermal Management: Incorporate thermal vias and heat sinks in rigid sections for high-power applications.
- Signal Integrity: Optimize trace widths and spacing to minimize signal loss in high-frequency designs.
Real-World Applications
Rigid-flex PCBs are revolutionizing modern electronics. For example:
- Medical Devices: Used in pacemakers and imaging equipment for compact, reliable designs.
- Automotive Electronics: Supports advanced driver-assistance systems (ADAS) in electric vehicles.
- 5G Technology: Enables high-density interconnects for antennas and base stations.
At JHYPCB, we recently delivered a 6-layer rigid-flex PCB for a wearable health monitor, achieving a 30% reduction in board thickness while maintaining signal integrity.
Industry Trends and Insights
The demand for rigid-flex PCBs is growing with the rise of IoT, 5G, and foldable electronics. According to industry reports, the global rigid-flex PCB market is expected to grow at a CAGR of 7.5% from 2023 to 2030. Designers are increasingly adopting HDI rigid-flex stackups to meet the needs of compact, high-performance devices.
Unique Design Tip
To optimize rigid-flex PCB stackups, consider using asymmetrical layer configurations. For instance, placing a single flexible layer between two rigid layers can reduce manufacturing costs while maintaining flexibility for 3D assemblies.
FAQs
What is the cost of a rigid-flex PCB?
Costs vary based on layer count, materials, and complexity. Contact us for a custom quote.
How do I choose the right layer count?
Single-sided or double-sided stackups suit simple designs, while multi-layer stackups are ideal for complex, high-density applications.
Conclusion
Rigid-flex PCB stackups offer unmatched flexibility and reliability for modern electronics. By understanding their features, types, and design considerations, you can unlock their potential for innovative applications. Ready to start your rigid-flex PCB project? Contact us for tailored solutions and expert support.
Rigid-Flex Board Stackup Design Guidelines and Helpful Resources
Related Posts
- Custom Flex PCB:Tailored Solutions for Your Applications
- Custom PCB Fabrication in China – Prototyping & Mass Production
- Expedited PCB Services – Quick Turnaround for Your Urgent Needs
- JHYPCB: The Best Prototype PCB Manufacturer for Your Needs
- Rapid PCB Prototyping Services: A Comprehensive Introduction
- Introduction to Semi-Flex PCBs: Bridging Rigid and Flex PCBs
- How to Select the Right Flexible PCB Manufacturer for Your Product: A 6-Step Guide
- What Are The Types of Flexible Circuit Boards?
- Why is Flexible PCB so Expensive?
- The Manufacturing Process Of Double-sided Flexible PCB Coverlay
- What Are The Advantages And Applications Of Rigid-Flex PCBs?
- Rigid PCB vs Flex PCB: What Is The Difference?
- How to Solder On Flex PCB?
- Flexible Printed Circuit For Today’s Packaging
- 16 Factors Affecting The Cost And Price of Flexible PCB
- Complete Introduction of Flexible Circuit Board Materials
- The terms you have to know related to the manufacture of Flexible PCB
- Knowledge of Flexible PCB Manufacturing Process Steps
- Knowledge of Plating on Flexible Circuit Board Surface
- Five factors that FPC PCB designers should know about impedance control
- Key Process Flow of Rigid-Fled PCB Production