Table of Contents
Why Choosing the Right Metal Core PCB Manufacturer is Critical to Your Success
In today’s fast-evolving electronics industry, metal core printed circuit boards (MCPCBs) have become essential for high-performance applications requiring superior heat dissipation. Unlike traditional FR4 boards, MCPCBs excel in managing thermal challenges, making them the go-to choice for industries like LED lighting, automotive electronics, and power supply systems. However, the success of your project hinges not only on the design of the PCB but also on selecting a reliable metal core PCB manufacturer. A trusted partner can ensure your boards meet stringent performance, quality, and durability standards, ultimately saving time and costs while enhancing your product’s reliability.
The Growing Demand for Metal Core PCBs
Metal core PCBs, often built with aluminum or copper bases, offer eight times better thermal conductivity than standard FR4 boards, enabling efficient heat transfer away from high-power components. This capability is critical in applications like LED PCBs, where excessive heat can reduce component lifespan or cause failures. With the rise of technologies such as 5G networks, electric vehicles (EVs), and renewable energy systems, the demand for MCPCBs is surging. According to industry trends, the global MCPCB market is projected to grow significantly, driven by the need for compact, high-efficiency electronics that operate reliably under demanding conditions.
Why the Right Manufacturer Matters
Choosing the right metal core PCB supplier is a pivotal decision that impacts your project’s outcome. A capable manufacturer provides not only high-quality boards but also expertise in material selection, prototyping, and production scalability. Key considerations include:
- Technical Expertise: Does the manufacturer understand your specific requirements, such as thermal conductivity, layer count, or surface finish?
- Customization Capabilities: Can they deliver tailored solutions for unique applications, from single-sided to multi-layer MCPCBs?
- Quality Assurance: Are their processes certified (e.g., ISO 9001) to ensure consistent performance and reliability?
- Timely Delivery: Can they meet your project deadlines with rapid prototyping and efficient production?
A misstep in selecting a manufacturer can lead to costly delays, subpar performance, or even product failures. For instance, a poorly made MCPCB may fail to dissipate heat effectively, compromising the longevity of high-power components like LEDs or power converters.
How JHYPCB Ensures Your Success
At JHYPCB, we specialize in delivering high-quality metal core PCBs, including aluminum PCBs and copper core PCBs, tailored to meet the needs of diverse industries. With over a decade of experience, we combine advanced manufacturing technology with rigorous quality control to ensure your PCBs perform flawlessly. Whether you need a single prototype or bulk production, our team is committed to supporting your project from design to delivery.
In the sections that follow, we’ll explore the unique advantages of MCPCBs, key factors in choosing a manufacturer, and practical tips for optimizing your PCB design. Read on to learn how to make informed decisions for your next project.

What is a Metal Core PCB?
MCPCBs are specialized circuit boards designed to excel in applications requiring exceptional thermal management. Unlike traditional FR4 boards, which rely on non-metallic substrates, MCPCBs use a metal base—typically aluminum or copper—to efficiently dissipate heat from high-power components. This unique construction makes metal core PCBs the preferred choice for industries such as LED lighting, automotive electronics, power supplies, and telecommunications, where reliability under high thermal loads is critical.
Key Characteristics of Metal Core PCBs
MCPCBs stand out due to their ability to handle heat-intensive environments. Their primary characteristics include:
- Superior Thermal Conductivity: The metal core, often aluminum or copper, transfers heat away from components up to eight times more effectively than FR4 boards. This ensures components remain cool, extending their lifespan.
- Durability in High Temperatures: MCPCBs can operate reliably in environments with elevated temperatures, reducing the risk of thermal failure.
- Compact Design: By efficiently managing heat, MCPCBs allow for denser component layouts without compromising performance, ideal for compact devices.
- Versatile Configurations: Available in single-sided, double-sided, and multi-layer designs, MCPCBs can be tailored to various applications.
These features make MCPCBs indispensable for applications where heat dissipation is a priority, such as aluminum PCBs for LED lighting or copper core PCBs for high-power converters.
Common Applications of Metal Core PCBs
The versatility of MCPCBs enables their use across a wide range of industries. Some key applications include:
- LED Lighting: MCPCBs are widely used in LED PCBs to manage heat generated by high-brightness LEDs, ensuring consistent performance and longevity.
- Automotive Electronics: In electric vehicles (EVs) and hybrid systems, MCPCBs support power modules and battery management systems, handling high thermal loads.
- Power Supplies and Converters: MCPCBs are critical in high-power circuits, such as DC-DC converters, where efficient heat dissipation prevents overheating.
- Telecommunications: With the rise of 5G infrastructure, MCPCBs are used in base stations and RF equipment to maintain performance under continuous operation.
Metal Core PCB vs. FR4: A Comparison
To understand the advantages of MCPCBs, it’s helpful to compare them with traditional FR4 boards. The table below highlights key differences:
Feature | Metal Core PCB | FR4 PCB |
---|---|---|
Base Material | Aluminum, copper, or alloy | Fiberglass-reinforced epoxy |
Thermal Conductivity | 1-8 W/m·K (high) | 0.25 W/m·K (low) |
Heat Dissipation | Excellent, ideal for high-power applications | Limited, prone to overheating |
Durability | High, withstands elevated temperatures | Moderate, degrades under high heat |
Applications | LEDs, automotive, power supplies | General electronics, low-power circuits |
This comparison underscores why MCPCBs are the go-to solution for heat-intensive applications, while FR4 boards are better suited for less demanding environments.
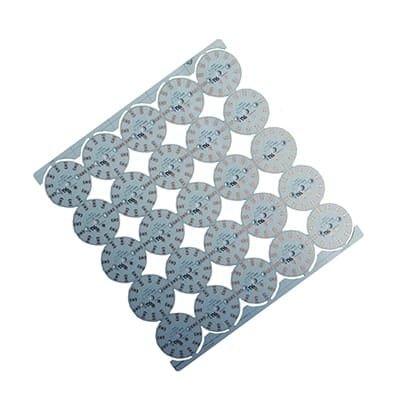
Key Factors in Choosing a Metal Core PCB Manufacturer
Selecting the right metal core PCB manufacturer is a critical step to ensure your project meets performance, quality, and timeline requirements. With the increasing demand for aluminum PCBs, copper core PCBs, and other MCPCBs in high-power applications, partnering with a reliable supplier can make or break your product’s success. This section outlines the essential factors to consider when evaluating a manufacturer, helping you make an informed decision for your LED PCB, automotive, or power supply projects.
1. Technical Expertise and Customization Capabilities
A competent manufacturer should have deep expertise in metal core PCB manufacturing and the ability to customize boards to your specific needs. Key technical aspects to evaluate include:
- Layer Count and Design Flexibility: Can the manufacturer produce single-sided, double-sided, or multi-layer MCPCBs to match your design requirements?
- Material Expertise: Do they offer a range of base materials, such as aluminum, copper, or specialized alloys, with varying thermal conductivity and glass transition temperature (Tg) options?
- Surface Finish Options: Are they equipped to provide finishes like HASL, Immersion Gold, or OSP to suit your application’s durability and performance needs?
Look for a manufacturer that collaborates closely with you during the design phase, offering guidance on optimizing board thickness, copper weight, and solder mask selection to ensure thermal efficiency and reliability.
2. Quality Certifications and Manufacturing Standards
Quality is non-negotiable in MCPCB production, as even minor defects can lead to thermal inefficiencies or circuit failures. Verify that the manufacturer adheres to industry standards, such as:
- ISO 9001 Certification: Ensures consistent quality management processes.
- UL Certification: Confirms compliance with safety and performance standards, critical for applications like LED lighting or automotive electronics.
- RoHS Compliance: Guarantees environmentally friendly materials, especially important for global markets.
A reputable manufacturer will also employ advanced inspection techniques, such as Automated Optical Inspection (AOI) and flying probe testing, to ensure every board meets your specifications.
3. Prototyping and Scalability
Before committing to large-scale production, prototyping is essential to validate your metal core PCB design. A reliable manufacturer should offer:
- Rapid Prototyping Services: The ability to produce small batches (as few as one board) for testing and refinement.
- Design Feedback: Expert advice to optimize your Gerber files, reducing costly revisions during bulk production.
- Scalability: Seamless transition from prototype to high-volume manufacturing without compromising quality or lead times.
Ask about the manufacturer’s prototyping process, including turnaround times and costs, to ensure it aligns with your project timeline.
4. Delivery Speed and Supply Chain Reliability
In fast-paced industries, timely delivery is critical. Evaluate the manufacturer’s ability to meet deadlines, especially for time-sensitive projects like 5G infrastructure or electric vehicle electronics. Consider:
- Lead Times: Can they provide quick turnaround for prototypes (e.g., 2-5 days) and bulk orders (e.g., 1-2 weeks)?
- Global Logistics: Do they have a robust supply chain to ensure consistent material availability and on-time delivery?
- Instant Quoting: Does the manufacturer offer online tools or rapid quote services to streamline the ordering process?
A manufacturer with a global presence and efficient logistics can minimize delays and keep your project on track.
5. Customer Support and Communication
Effective communication is vital for a successful partnership. Look for a manufacturer that provides:
- Technical Support: Access to engineers who can answer questions about materials, design, or manufacturing processes.
- 24/7 Customer Service: Responsive support, especially for international clients across different time zones.
- Transparent Communication: Clear updates on order status, from prototype to delivery.
A manufacturer that prioritizes customer support can help you navigate complex design challenges and ensure your requirements are met.
Checklist for Choosing a Metal Core PCB Manufacturer
To simplify your decision-making process, use this checklist when evaluating potential suppliers:
- Offers expertise in aluminum and copper core PCBs for your application.
- Provides customizable options for layer count, thickness, and surface finish.
- Holds certifications like ISO 9001, UL, or RoHS.
- Supports rapid prototyping with actionable design feedback.
- Guarantees reliable delivery with transparent lead times.
- Offers responsive customer support and technical guidance.
By partnering with a manufacturer that meets these criteria, you can ensure your metal core PCBs are built to perform reliably in demanding applications.
Choosing the right MCPCB supplier is about more than just technical capabilities—it’s about finding a partner who aligns with your project goals. In the next section, we’ll dive into the importance of metal core PCB prototyping and how it can save time and costs by refining your design before full-scale production.
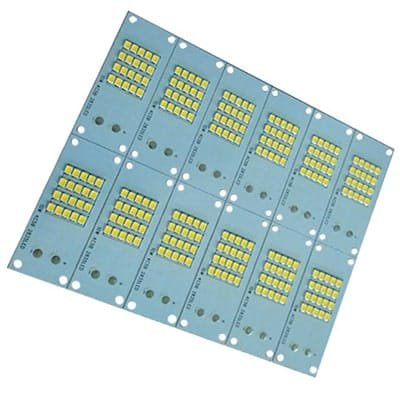
The Importance of Metal Core PCB Prototyping
Prototyping is a critical step in the development of metal core PCBs, ensuring your design performs reliably before committing to full-scale production. For high-performance applications like LED PCBs, automotive electronics, or power converters, a metal core PCB prototype allows you to validate thermal management, electrical performance, and design accuracy. This section explores why prototyping is essential, what factors to consider, and how to collaborate with your manufacturer to achieve optimal results.
Why Prototyping Matters for MCPCBs
Creating a prototype before bulk manufacturing offers several key benefits:
- Design Validation: A prototype lets you test your MCPCB design under real-world conditions, ensuring it meets thermal and electrical requirements. For example, in aluminum PCB prototyping for LED applications, you can verify heat dissipation to prevent component overheating.
- Cost Efficiency: Identifying and fixing design flaws early reduces the risk of costly revisions during mass production. A single prototype can save thousands in rework costs.
- Performance Optimization: Prototyping allows you to tweak parameters like board thickness, copper weight, or solder mask to enhance performance for specific applications.
- Risk Mitigation: By testing a prototype, you can address potential issues, such as poor layer adhesion or inadequate thermal conductivity, before they impact your final product.
Skipping the prototyping phase can lead to expensive delays or product failures, especially in heat-sensitive applications like copper core PCBs for power supplies.
Key Parameters to Define for Your MCPCB Prototype
To ensure your prototype meets your project’s needs, clearly communicate the following specifications to your manufacturer:
- Layer Configuration: Specify whether you need a single-sided, double-sided, or multi-layer MCPCB, depending on your circuit complexity.
- Base Material: Choose the appropriate metal core (e.g., aluminum for cost-effectiveness or copper for superior thermal conductivity) based on your application’s thermal demands.
- Board Thickness: MCPCBs typically range from 30 to 130 mil. Thicker boards offer better heat dissipation but may increase costs.
- Copper Weight: Select a copper thickness (e.g., 1 oz to 3 oz) to balance conductivity and cost.
- Surface Finish: Options like HASL, Immersion Gold, or OSP impact solderability and durability. For example, Immersion Gold is ideal for high-reliability applications.
- Solder Mask: While white is standard for MCPCBs due to its reflective properties in LED applications, confirm if other colors are available for specific needs.
Providing detailed Gerber files and discussing these parameters with your manufacturer ensures the prototype aligns with your design goals.
Collaborating with Your Manufacturer
Effective collaboration with your MCPCB supplier during prototyping can streamline the process. Here’s how to maximize the partnership:
- Share Detailed Requirements: Provide comprehensive design files, including schematics and bill of materials (BOM), to avoid miscommunication.
- Request Design Feedback: Ask the manufacturer to review your design for manufacturability, as they may suggest optimizations to improve performance or reduce costs.
- Evaluate Turnaround Time: Ensure the manufacturer offers rapid prototyping (e.g., 2-5 days) to keep your project on schedule.
- Test and Iterate: Use prototype testing results to refine your design. If issues arise, work with the manufacturer to order revised prototypes quickly.
A manufacturer with strong technical support can guide you through the prototyping process, helping you achieve a design that’s ready for production.
Common Prototyping Challenges and Solutions
Prototyping can encounter challenges, but proactive planning can address them:
- Challenge: Inaccurate thermal performance due to improper material selection.
Solution: Consult with your manufacturer to select a base material with the appropriate thermal conductivity (e.g., copper for high-power applications). - Challenge: High prototyping costs for small batches.
Solution: Choose a manufacturer that supports low minimum order quantities (MOQs), such as a single board. - Challenge: Delays in prototype delivery.
Solution: Partner with a supplier offering fast turnaround and transparent communication on lead times.
Addressing these challenges early ensures a smoother transition to bulk production.
A successful metal core PCB prototype paves the way for efficient, high-quality manufacturing. By validating your design and refining specifications, you can confidently scale up production without unexpected setbacks. In the next section, we’ll explore the materials used in MCPCBs, including how to choose the right base material for your project’s performance and cost requirements.

Material Selection for Metal Core PCBs
The choice of materials is a pivotal factor in the performance of MCPCBs, particularly for applications requiring superior thermal management, such as LED lighting, automotive electronics, and power supplies. The base material of an MCPCB—typically aluminum, copper, or specialized alloys—directly impacts its thermal conductivity, durability, and cost. This section explores the most common materials used in MCPCB manufacturing, their properties, and how to select the right material for your project’s specific needs.
Common Base Materials for MCPCBs
MCPCBs rely on a metal core to dissipate heat efficiently. The most widely used base materials include:
- Aluminum: The most popular choice for aluminum PCBs due to its balance of cost, thermal conductivity (1-2 W/m·K), and lightweight properties. Aluminum is ideal for applications like LED lighting and consumer electronics, where cost-effectiveness is a priority.
- Copper: Offers superior thermal conductivity (3-8 W/m·K) compared to aluminum, making copper core PCBs suitable for high-power applications like power converters and automotive power modules. However, copper is heavier and more expensive.
- Alloys: Specialized blends, such as aluminum-copper composites, combine the benefits of both metals. These are used in niche applications requiring tailored thermal and mechanical properties.
Each material has unique characteristics, and selecting the right one depends on your project’s thermal, electrical, and budgetary requirements.
Key Material Properties to Consider
When choosing a base material for your metal core PCB, evaluate the following properties:
- Thermal Conductivity: Measured in W/m·K, this determines how efficiently the material transfers heat away from components. For example, copper’s higher conductivity makes it ideal for high-power circuits, while aluminum suffices for moderate thermal loads.
- Glass Transition Temperature (Tg): The Tg value indicates the temperature at which the material begins to lose its mechanical stability. Higher Tg materials (e.g., 130°C or above) are essential for applications operating in high-temperature environments.
- Dielectric Layer Performance: The dielectric layer between the metal core and copper circuitry affects insulation and thermal transfer. A high-quality dielectric ensures efficient heat dissipation while maintaining electrical isolation.
- Weight and Cost: Aluminum is lighter and more cost-effective, while copper offers better performance at a higher cost and weight. Alloys may provide a middle ground but require careful evaluation.
Understanding these properties helps you align the material choice with your application’s performance goals.
Material Selection Guide by Application
Different applications demand specific material properties. Below is a guide to help you choose the right base material:
Application | Recommended Material | Why? |
---|---|---|
LED Lighting | Aluminum | Cost-effective, sufficient thermal conductivity for LED heat dissipation. |
Automotive Electronics | Copper or Alloys | High thermal conductivity for power modules and battery management. |
Power Supplies/Converters | Copper | Superior heat dissipation for high-power, continuous-operation circuits. |
Telecommunications (5G) | Aluminum or Alloys | Balances cost and performance for RF equipment and base stations. |
Discuss your application with your manufacturer to confirm the material’s suitability, especially if your project involves unique environmental or performance constraints.
Practical Tips for Choosing MCPCB Materials
To ensure the best material selection for your MCPCB design, consider these practical steps:
- Define Thermal Requirements: Calculate the heat output of your components (e.g., LEDs or power transistors) to determine the required thermal conductivity.
- Assess Environmental Conditions: Consider operating temperatures, humidity, and mechanical stress to select a material with appropriate Tg and durability.
- Balance Cost and Performance: For budget-sensitive projects, aluminum may suffice, while high-performance applications may justify copper’s higher cost.
- Consult Your Manufacturer: Engage with your MCPCB supplier to verify material availability and compatibility with your design specifications, such as layer count or surface finish.
A collaborative approach with your manufacturer can help you avoid common pitfalls, such as selecting a material with insufficient thermal performance or excessive cost.
Choosing the right material for your metal core PCB lays the foundation for optimal thermal management and long-term reliability. In the next section, we’ll explore the MCPCB manufacturing process, detailing the steps involved in transforming your design into a high-quality, functional board.
Detailed Metal Core PCB Manufacturing Process
The metal core PCB (MCPCB) manufacturing process transforms a carefully designed schematic into a high-performance circuit board capable of efficient heat dissipation for applications like LED lighting, automotive electronics, and power supplies. While similar to standard PCB production, MCPCB manufacturing involves unique considerations due to its metal base, typically aluminum or copper. This section provides a step-by-step overview of the MCPCB manufacturing process, highlighting key stages and their importance to ensure quality and reliability.
Step 1: Design Review and Preparation
The process begins with a thorough review of your Gerber files and design specifications. Manufacturers verify the design for manufacturability, checking parameters like layer count, board thickness, copper weight, and material compatibility. This step ensures the design aligns with the capabilities of aluminum PCB or copper core PCB production, minimizing errors during manufacturing.
- Key Considerations: Ensure your Gerber files include precise details on the metal core type, dielectric layer, and surface finish requirements.
- Output: A validated design ready for fabrication.
Step 2: Material Cutting and Drilling
Once the design is approved, the metal core material (e.g., aluminum or copper) is cut into panels of the specified size. Automated machines then drill precise holes, including vias, to facilitate component placement and interlayer connections.
- Why It Matters: Accurate drilling ensures proper alignment of components and reliable electrical pathways.
- Unique to MCPCBs: The metal core requires specialized drilling techniques to avoid damaging the material while maintaining precision.
Step 3: Electroplating and Copper Plating
Electroplating creates conductive pathways by depositing a thin layer of copper in the drilled vias, connecting the layers of the MCPCB. This is followed by copper plating, where additional copper is applied to the board’s surface to achieve the desired thickness (e.g., 1-3 oz) for optimal conductivity.
- Why It Matters: Copper plating enhances electrical performance and supports high-current applications, critical for MCPCB applications like power converters.
- Unique to MCPCBs: The metal core’s thermal properties require careful control to ensure the dielectric layer maintains insulation during plating.
Step 4: Circuit Pattern Imaging and Etching
The circuit pattern is created using a photoresist film, which is applied to the copper surface and exposed to UV light through a photo negative (film) of the PCB design. This process defines the conductive paths. Excess copper is then removed through chemical etching, leaving only the desired circuit traces.
- Why It Matters: Precise imaging and etching ensure the circuit matches your design, avoiding short circuits or open connections.
- Unique to MCPCBs: The white solder mask, common in MCPCBs for LED applications, is often applied post-etching to enhance reflectivity and insulation.
Step 5: Solder Mask and Silkscreen Application
A solder mask, typically white for MCPCBs, is applied to insulate the conductive traces and protect the board from environmental damage. The silkscreen layer follows, adding labels, component identifiers, and other markings for assembly guidance.
- Why It Matters: The solder mask prevents unintended electrical connections, while the silkscreen improves assembly accuracy.
- Unique to MCPCBs: The white solder mask is standard due to its reflective properties, particularly for LED PCBs, but other colors may be available for specific applications.
Step 6: Surface Finish Application
To protect the exposed copper from oxidation and ensure solderability, a surface finish is applied. Common options for MCPCBs include:
HASL (Hot Air Solder Leveling): Cost-effective, widely used for general applications.
Immersion Gold: Offers excellent corrosion resistance, ideal for high-reliability applications like automotive electronics.
OSP (Organic Solderability Preservative): A thin, eco-friendly coating for short-term protection.
Why It Matters: The surface finish enhances durability and ensures reliable soldering during assembly.
Step 7: Inspection and Testing
Automated inspection tools, such as Automated Optical Inspection (AOI) and flying probe testers, verify the board’s integrity, checking for defects like misaligned traces or incomplete vias. Manual inspections by experts may also be conducted to ensure compliance with your specifications.
- Why It Matters: Rigorous testing guarantees the MCPCB meets performance and reliability standards, reducing the risk of failures in high-power applications.
Step 8: Final Preparation and Packaging
After passing inspection, the boards are cleaned, cut to their final dimensions, and packaged for delivery. Manufacturers ensure proper handling to prevent damage to the metal core or delicate circuitry.
- Why It Matters: Proper packaging ensures the boards arrive in pristine condition, ready for assembly or further testing.
Why Understanding the Process Matters
Familiarity with the MCPCB manufacturing process empowers you to communicate effectively with your manufacturer, ensuring your design specifications are met. By understanding each step, you can make informed decisions about materials, tolerances, and testing requirements. In the next section, we’ll explore metal core PCB pricing and quoting, providing insights on how to budget effectively for your project.
Metal Core PCB Pricing and Quoting Process
Understanding the cost of metal core PCBs (MCPCBs) is essential for budgeting and planning high-performance projects like LED lighting, automotive electronics, or power supplies. The price of MCPCBs varies based on several factors, including design complexity, materials, and production volume. Equally important is a streamlined quoting process that provides transparency and efficiency. This section explores the key factors influencing MCPCB costs, offers tips for cost optimization, and outlines how to obtain an accurate quote from your manufacturer.
Factors Influencing Metal Core PCB Costs
The cost of an MCPCB depends on multiple variables, each tied to the design and manufacturing requirements. Key factors include:
- Board Complexity and Layer Count: Single-sided MCPCBs are less expensive than double-sided or multi-layer boards due to simpler manufacturing processes.
- Base Material: Aluminum PCBs are generally more cost-effective than copper core PCBs, which have higher thermal conductivity but increase material costs.
- Board Size and Thickness: Larger boards or those with thicker metal cores (e.g., 30-130 mil) require more material, raising costs.
- Copper Weight: Thicker copper layers (e.g., 2-3 oz) improve conductivity but increase expenses compared to standard 1 oz layers.
- Surface Finish: Options like Immersion Gold are pricier than HASL but offer superior durability for applications like automotive MCPCBs.
- Production Volume: Low-volume prototypes have a higher per-unit cost, while bulk orders benefit from economies of scale.
- Additional Features: Special requirements, such as custom dielectric layers or high-Tg materials, can add to the cost.
Understanding these factors helps you make informed decisions to balance performance and budget.
Tips for Optimizing MCPCB Costs
To achieve cost-effective metal core PCB production without compromising quality, consider the following strategies:
- Optimize Design for Manufacturability: Simplify your design by minimizing layer count or board size where possible. Consult your manufacturer for design feedback to eliminate unnecessary complexity.
- Choose the Right Material: Select aluminum for cost-sensitive applications like LED lighting, reserving copper for high-power projects where superior thermal performance is critical.
- Leverage Bulk Ordering: Order larger quantities to reduce per-unit costs, especially for proven designs after successful prototyping.
- Standardize Specifications: Use standard board thicknesses (e.g., 1.6 mm) and copper weights (e.g., 1 oz) to avoid premium charges for custom configurations.
- Plan for Prototyping: Invest in a prototype to refine your design early, preventing costly revisions during bulk production.
By implementing these strategies, you can significantly reduce costs while maintaining the performance of your MCPCB design.
The Quoting Process: What to Provide
Obtaining an accurate quote for your metal core PCB requires clear communication with your manufacturer. Most suppliers, including those specializing in aluminum PCB manufacturing, offer rapid quoting systems, delivering estimates within 2-24 hours. To ensure precision, provide the following information:
- Gerber Files: Complete design files detailing the board layout, layer stack-up, and component placement.
- Bill of Materials (BOM): A list of components, if applicable, to clarify assembly requirements.
- Specifications: Details on layer count, board dimensions, material type (aluminum, copper, or alloy), copper weight, surface finish, and solder mask (typically white for MCPCBs).
- Quantity: Specify whether you need a prototype (e.g., 1-10 boards) or bulk production (e.g., 100+ boards).
- Delivery Timeline: Indicate your desired lead time to align with project deadlines.
- Special Requirements: Note any unique needs, such as high-Tg materials or specific testing protocols.
Providing comprehensive details ensures the quote reflects your project’s exact needs, avoiding surprises during production.
Why Transparent Pricing Matters
A transparent quoting process builds trust and helps you plan effectively. Look for a manufacturer that offers:
- Instant or Rapid Quotes: Online tools or quick responses (within 24 hours) streamline budgeting.
- Detailed Cost Breakdown: Clarity on how material, labor, and additional features contribute to the total cost.
- Flexibility for Changes: The ability to revise quotes if specifications change, ensuring alignment with your evolving needs.
Transparent pricing empowers you to make data-driven decisions, ensuring your MCPCB project stays within budget while meeting performance goals.
Why Choose JHYPCB for Your Metal Core PCB Needs
When it comes to metal core PCB manufacturing, partnering with a trusted and experienced supplier is critical to ensuring your project’s success. JHYPCB stands out as a leading provider of aluminum PCBs, copper core PCBs, and other MCPCBs, offering tailored solutions for applications like LED lighting, automotive electronics, and power supplies. With a commitment to quality, customization, and customer satisfaction, JHYPCB delivers high-performance boards that meet the demands of even the most challenging projects. This section highlights why JHYPCB is the ideal choice for your MCPCB needs.
1. Comprehensive MCPCB Solutions
JHYPCB offers a full range of metal core PCB services, catering to diverse industries and project requirements:
- Wide Material Options: From cost-effective aluminum to high-performance copper cores, JHYPCB provides materials tailored to your thermal and electrical needs.
- Flexible Configurations: Whether you need single-sided, double-sided, or multi-layer MCPCBs, JHYPCB supports designs of varying complexity.
- Custom Prototyping: Start with as few as one prototype board to validate your design, ensuring a smooth transition to bulk production.
- Specialized Applications: Expertise in LED PCBs, automotive power modules, and telecommunications equipment, delivering boards optimized for high-power environments.
This versatility ensures JHYPCB can meet the unique demands of your project, no matter the scale or complexity.
2. Uncompromising Quality and Certifications
Quality is at the core of JHYPCB’s operations. The company adheres to stringent industry standards to deliver reliable and durable MCPCBs:
- ISO 9001:2008 Certification: Ensures consistent quality management across all manufacturing processes.
- UL and RoHS Compliance: Guarantees safe, environmentally friendly boards suitable for global markets.
- Advanced Testing: Utilizes Automated Optical Inspection (AOI) and flying probe testing to verify board integrity, minimizing defects and ensuring performance.
These certifications and rigorous testing protocols give you confidence that your MCPCBs will perform reliably in demanding applications.
3. Rapid Turnaround and Scalability
Time is critical in today’s fast-paced industries. JHYPCB excels in delivering metal core PCBs on schedule without compromising quality:
- Fast Prototyping: Turnaround times as short as 2-5 days for prototypes, enabling rapid design validation.
- Scalable Production: Seamless transition from small-batch prototyping to high-volume manufacturing, supporting quantities from one board to thousands.
- Efficient Logistics: Global supply chain and reliable delivery ensure your boards arrive on time, even for time-sensitive projects like 5G infrastructure or electric vehicle electronics.
JHYPCB’s streamlined processes keep your project on track, from initial design to final delivery.
4. Exceptional Customer Support
JHYPCB prioritizes customer satisfaction with responsive and expert support:
- 24/7 Online Support: Access to technical experts and customer service representatives, available across time zones to address your questions.
- Design Consultation: Engineers provide feedback on your MCPCB design, optimizing for manufacturability and performance.
- Instant Quoting: Online tools deliver accurate quotes within 2-24 hours, simplifying budgeting and planning.
This dedication to customer service ensures a collaborative partnership, helping you navigate complex design challenges with ease.
5. Competitive Pricing and Value
JHYPCB offers cost-effective solutions without sacrificing quality. By optimizing manufacturing processes and offering flexible MOQs (minimum order quantities), JHYPCB caters to both small startups and large enterprises. Whether you need a single aluminum PCB prototype or bulk copper core PCBs, JHYPCB provides transparent pricing and tailored solutions to maximize value.
Partner with JHYPCB Today
With a proven track record in MCPCB manufacturing, JHYPCB is your trusted partner for delivering high-quality, reliable boards tailored to your needs. Ready to start your project? Contact JHYPCB for a free quote within 24 hours or explore our services to see how we can support your next LED PCB or automotive MCPCB project.
Frequently Asked Questions About Metal Core PCBs
Navigating the complexities of metal core PCB (MCPCB) design and manufacturing can raise many questions, especially for engineers and procurement managers working on high-performance applications like LED lighting, automotive electronics, or power supplies. This section addresses common questions about MCPCBs, providing clear, concise answers to help you make informed decisions for your project.
1. What is the difference between a metal core PCB and a standard FR4 PCB?
Metal core PCBs (MCPCBs) use a metal base, typically aluminum or copper, to enhance heat dissipation, making them ideal for high-power applications. In contrast, FR4 PCBs use a fiberglass-reinforced epoxy base, which has lower thermal conductivity (0.25 W/m·K vs. 1-8 W/m·K for MCPCBs). MCPCBs are better suited for applications like LED PCBs or power converters, where heat management is critical, while FR4 boards are used for general electronics with lower thermal demands.
2. When should I choose an aluminum PCB over a copper core PCB?
3. How long does it take to prototype a metal core PCB?
Prototyping timelines vary by manufacturer and design complexity. For MCPCB prototyping, reputable suppliers typically deliver prototypes in 2-5 days for simple designs (e.g., single-sided aluminum PCBs) and up to 7-10 days for multi-layer boards. Providing complete Gerber files and clear specifications can expedite the process.
4. What surface finish is best for my MCPCB?
The choice of surface finish depends on your application:
- HASL (Hot Air Solder Leveling): Cost-effective, suitable for general applications but less precise for fine-pitch components.
- Immersion Gold: Offers excellent corrosion resistance and solderability, ideal for high-reliability applications like automotive MCPCBs.
- OSP (Organic Solderability Preservative): Eco-friendly and cost-effective for short-term storage but less durable.
Discuss your project’s durability and soldering needs with your manufacturer to select the best option.
5. Why is the solder mask typically white for MCPCBs?
White solder masks are standard for MCPCBs, especially in LED PCB applications, because they reflect light, enhancing brightness and efficiency in lighting systems. Other colors (e.g., green or black) are available but less common, as they may absorb light or heat, reducing performance in certain applications.
6. How can I reduce the cost of my MCPCB project?
To lower metal core PCB costs, consider these strategies:
- Use aluminum instead of copper for cost-sensitive projects.
- Simplify your design by minimizing layer count or board size.
- Order in bulk to benefit from economies of scale.
- Work with your manufacturer to optimize for manufacturability, reducing unnecessary features.
Prototyping early can also prevent costly revisions during production.
7. What certifications should I look for in an MCPCB manufacturer?
Ensure your manufacturer holds:
- ISO 9001: Guarantees consistent quality management.
- UL Certification: Confirms safety and performance standards, critical for applications like LED lighting.
- RoHS Compliance: Ensures environmentally friendly materials, essential for global markets.
These certifications indicate a commitment to quality and reliability.
8. Can MCPCBs be used in high-temperature environments?
9. How do I start my MCPCB project?
Begin by preparing your design files (e.g., Gerber files, BOM) and defining specifications like layer count, material, and surface finish. Contact a trusted MCPCB supplier for a quote, ideally one offering rapid prototyping and technical support. For example, JHYPCB provides instant quotes and expert guidance to kickstart your project.
Industry Trends and the Future of Metal Core PCBs
As technology advances, metal core printed circuit boards (MCPCBs) are playing an increasingly vital role in high-performance electronics, driven by their superior thermal management capabilities. From LED lighting to electric vehicles (EVs) and 5G infrastructure, MCPCBs are at the forefront of enabling efficient, reliable, and compact solutions. This section explores the latest industry trends shaping the demand for MCPCBs and offers insights into their future applications, helping you stay ahead in your project planning.
1. Rising Demand in Electric Vehicles and Renewable Energy
The global push for sustainability is fueling the growth of MCPCBs in electric vehicle electronics and renewable energy systems. EVs rely on power modules, battery management systems, and charging infrastructure that generate significant heat, requiring aluminum PCBs or copper core PCBs for efficient thermal dissipation. Similarly, solar inverters and wind energy converters use MCPCBs to ensure reliability under high-power conditions. As the EV market is projected to grow at a CAGR of over 20% through 2030, the demand for MCPCBs in these applications is set to soar.
2. Expansion in 5G and Telecommunications
The rollout of 5G networks is driving the need for compact, high-performance electronics capable of continuous operation. MCPCBs are critical in 5G base stations, RF modules, and antennas, where they manage heat from high-frequency components. Their ability to support dense circuit designs while maintaining thermal stability makes them ideal for next-generation telecommunications. As 5G adoption accelerates, manufacturers are innovating with high-Tg materials and advanced dielectric layers to meet these demanding requirements.
3. Advancements in LED Lighting Technology
LED PCBs remain a cornerstone of MCPCB applications, with innovations in smart lighting and high-brightness LEDs increasing demand. MCPCBs, particularly aluminum PCBs, are essential for dissipating heat in automotive headlights, street lighting, and architectural illumination. Emerging trends like tunable white LEDs and IoT-integrated lighting systems require MCPCBs with enhanced thermal conductivity and compact designs, pushing manufacturers to develop thinner, more efficient boards.
4. Focus on Sustainable and Eco-Friendly Materials
Environmental regulations and consumer demand for sustainability are shaping MCPCB production. Manufacturers are adopting RoHS-compliant materials and exploring recyclable metal cores to reduce environmental impact. Additionally, advancements in low-energy manufacturing processes and eco-friendly surface finishes, such as OSP, are gaining traction. These trends align with global efforts to create greener electronics, particularly in markets like Europe and North America.
5. Integration with AI and IoT Devices
The rise of artificial intelligence (AI) and Internet of Things (IoT) devices is creating new opportunities for MCPCBs. AI-powered systems, such as edge computing devices, generate significant heat due to high processing demands, making copper core PCBs a preferred choice. Similarly, IoT devices, like smart sensors and wearables, require compact MCPCBs to balance thermal performance with space constraints. As these technologies proliferate, MCPCB designs are evolving to support smaller footprints and higher power densities.
Preparing for the Future
To leverage these trends, consider the following strategies for your MCPCB projects:
- Adopt High-Performance Materials: Choose copper or advanced alloys for applications like EVs or AI systems, where thermal demands are extreme.
- Prioritize Compact Designs: Work with manufacturers to develop thinner MCPCBs for IoT and 5G applications without sacrificing performance.
- Embrace Sustainability: Select suppliers offering RoHS-compliant and recyclable materials to meet regulatory and market expectations.
- Stay Agile: Partner with a manufacturer that invests in R&D to keep pace with emerging technologies and industry standards.
By aligning your project with these trends, you can ensure your MCPCBs are future-proof and competitive in rapidly evolving markets.
Partner with JHYPCB for Cutting-Edge MCPCBs
At JHYPCB, we stay ahead of industry trends by offering innovative metal core PCB solutions tailored to applications like 5G, EVs, and smart lighting. Our commitment to quality, rapid prototyping, and sustainable practices ensures your project thrives in today’s dynamic landscape. Contact us today for a free quote and discover how we can support your next MCPCB project.
Advanced Learning: